Reading time: 9 minutes
‘Life’, 24-year-old Corinna pauses for a moment, ‘life is circular and cyclical by nature, and is characterized by a constant change between becoming and passing, being born and dying.’ Corinna is a trainee teacher in Munich and, as part of her career orientation, is trying to give 15-year-old local students an idea of how ecological thinking can be applied to the production of goods. ‘This circularity makes it clear’, she continues, ‘why our current economic system is in such conflict with our planet. While nature builds harmony in closed cycles, the economy strives for infinite growth.’
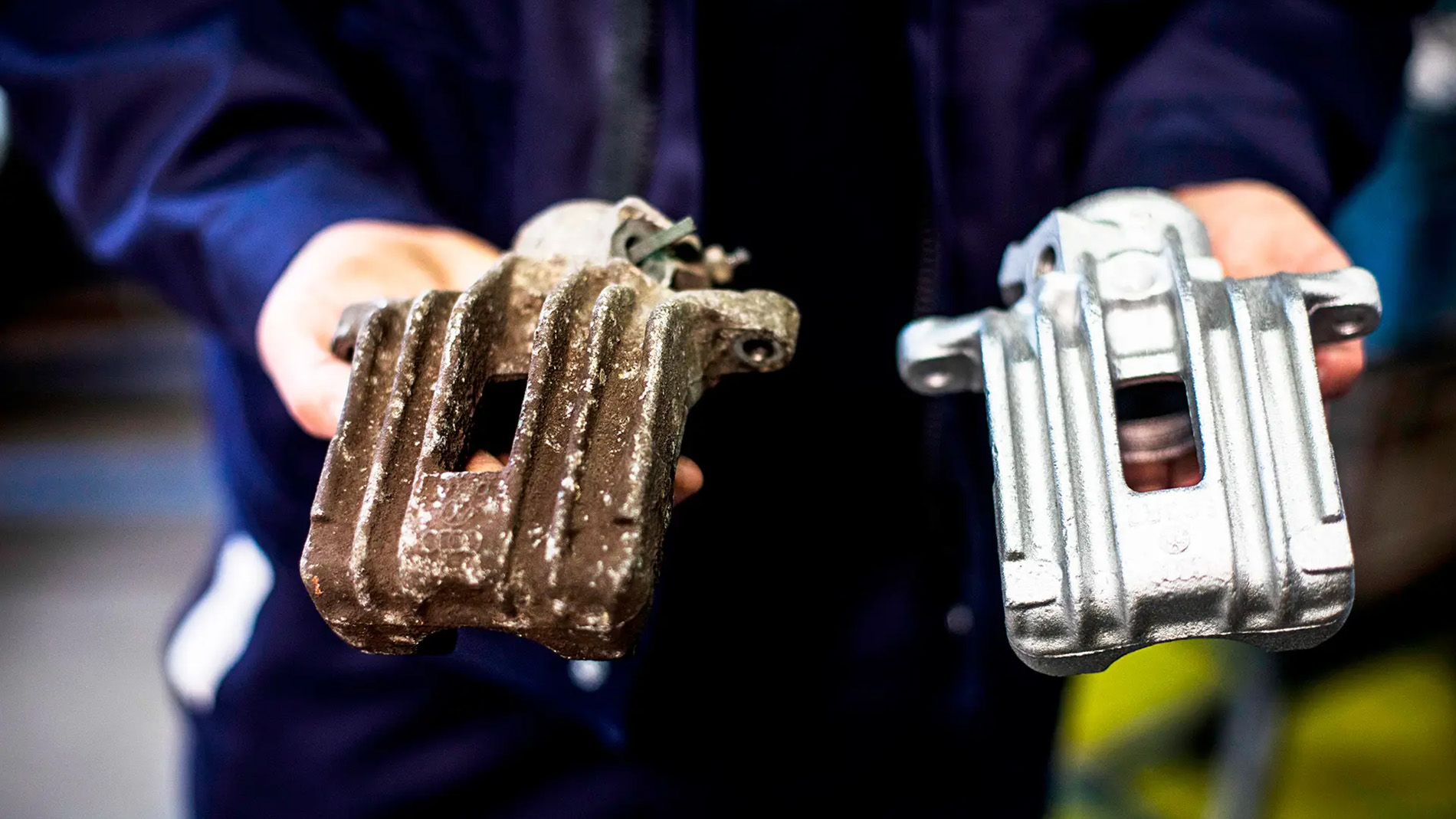
‘Everything starts with a core’ is a similarly overarching principle of the European Remanufacturing Association APRA. ‘Core’ is the standardized term for the used part or component intended for remanufacturing, specially identified and protected for that purpose. APRA (Automotive Parts Remanufacturers Association) has made an outstanding contribution to the development of international standards and language regulations for companies wishing to operate safely in the complex, global world of remanufacturing.
A core is not waste or scrap, but holds a high value. And just as you don't just throw away a plastic bottle, Corinna’s students will soon learn that the production and operation of cars, for example, needn’t be as incompatible with the environment as is currently assumed. In any case, there will be no shortage of valuable ‘cores’.
More than one million ‘cores’ are stored in Northern Europe's largest ‘core warehouse’ in Poland, which BORG Automotive Reman opened in 2014. Every year, BORG remanufactures more than two million units across all manufacturers. With production facilities in England, Poland and Spain as well as warehouses across Europe, BORG distributes cores under four brands. BORG began remanufacturing almost 50 years ago, at a time when defective appliances were considered scrap and a burden to the environment. Today, an increasing number of automotive companies and their suppliers recognize that remanufacturing is a significant strategy for climate protection.
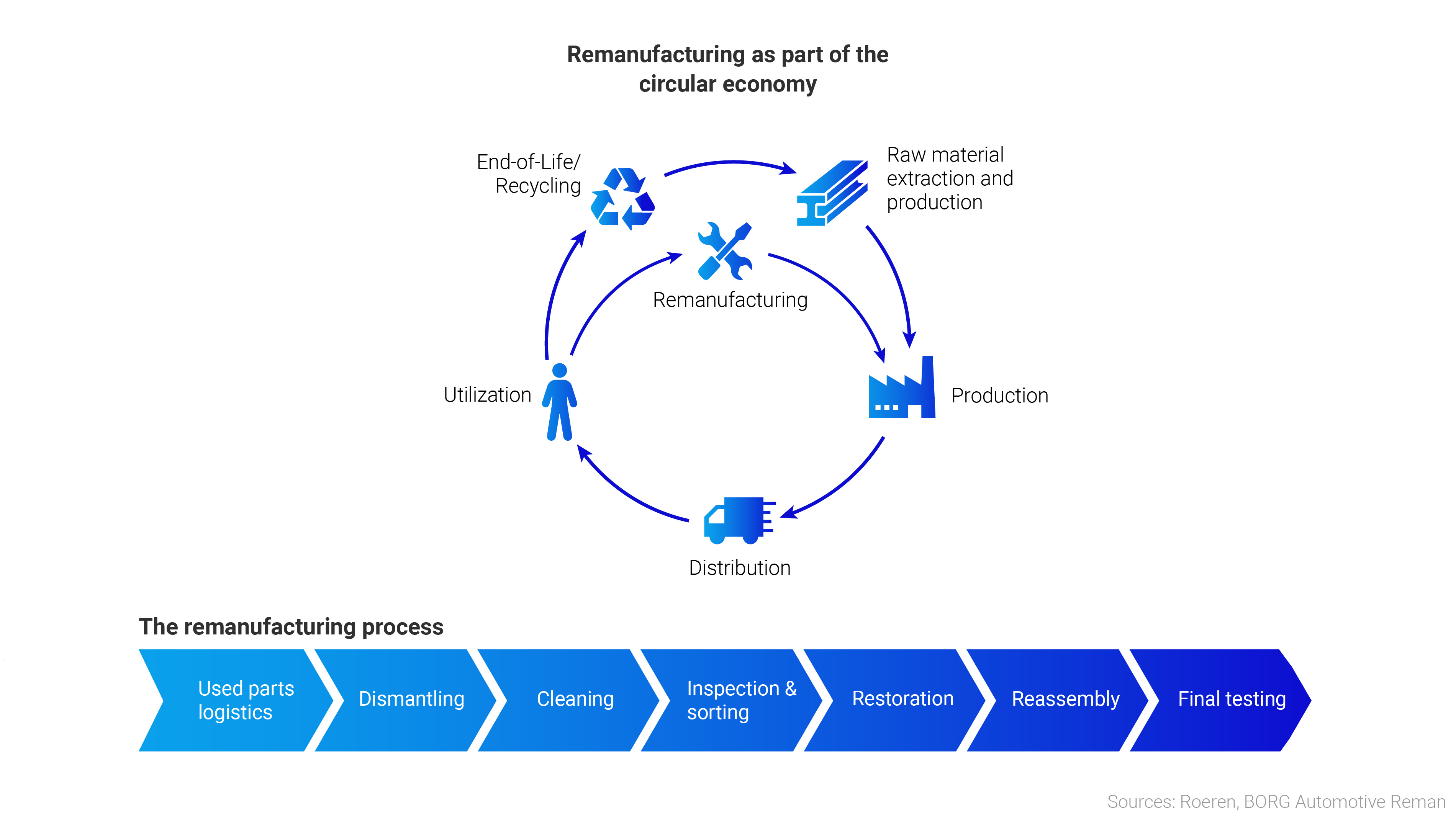

‘Remanufacturing in the automotive aftermarket has become a model for successful and sustainable business practices, including those in non-automotive sectors’, says Peter Bartel, Head of Marketing at Circular Economy Solutions GmbH (C-ECO). C-ECO advises companies that want to expand their circular economy activities in the automotive aftermarket. ‘Many aspects of the circular economy have been technically solved, but there is a lack of established business models.’
‘Remanufacturing in the automotive aftermarket has become a model for successful and sustainable business practices, including those in non-automotive sectors.’
Peter Bartel, Head of Marketing, Circular Economy Solutions GmbH
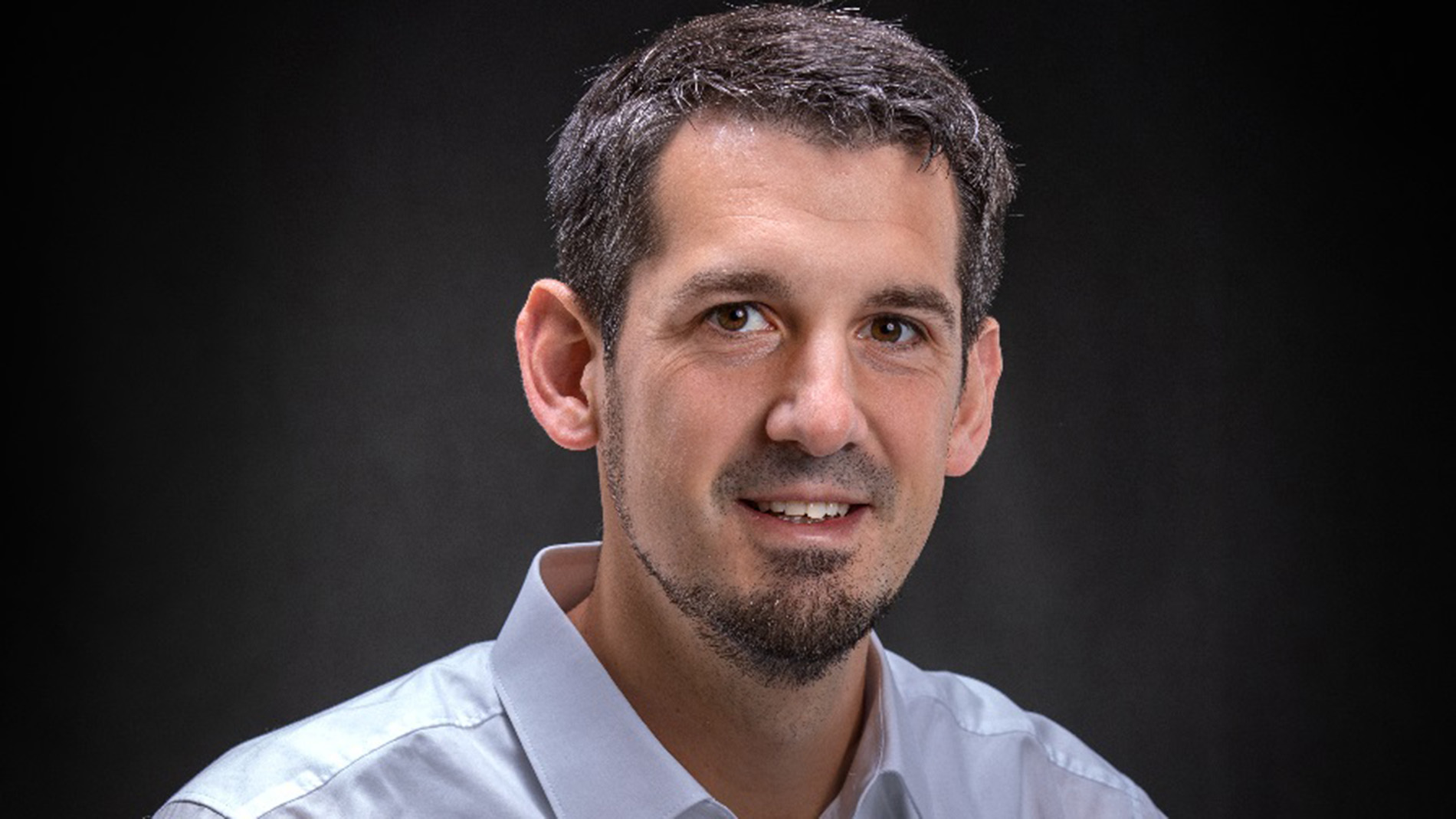
Remanufacturing is a key part of the circular economy, which is becoming an increasingly important topic in the automotive industry. The industry hopes to meet emission targets such as the UN Sustainable Development Goals (SDGs), or achieve them more quickly. ‘The earlier you start with circularity, the sooner you will gain advantages—Instead of having to buy certificates at some point, which are becoming increasingly expensive’, says Stefan Caba of engineering service provider EDAG Engineering GmbH.
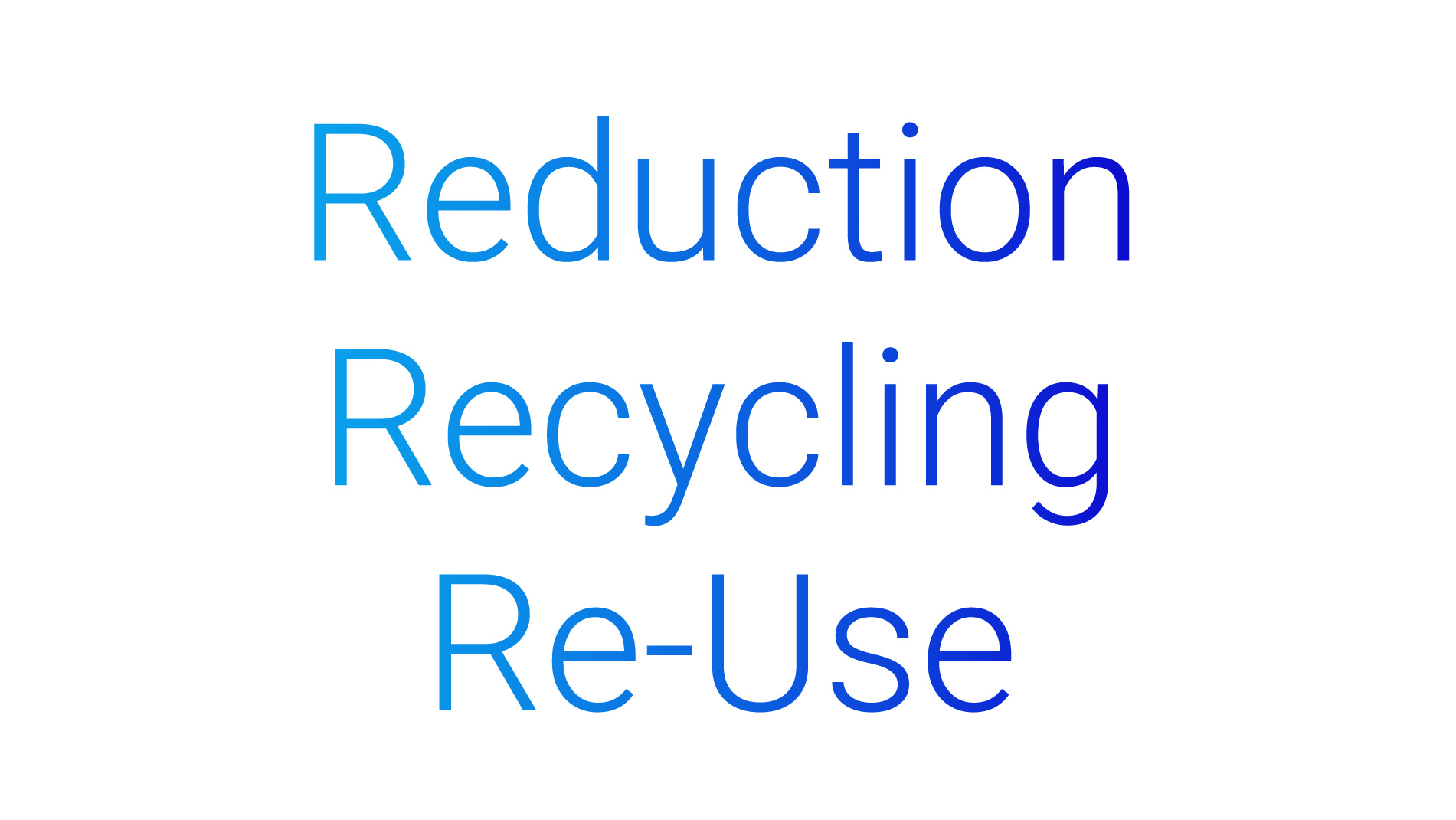
Reduce, recycle, and reuse are the three core principles of the circular economy that Caba uses to advise his clients on their sustainability investments. ‘It is more cost-effective in the long term to invest in sustainable solutions than to offset emissions at a late stage’, says Caba optimistically. In stages two and three, recycling and reuse, remanufacturing is the best-documented sustainability discipline. It has long had standardized industrial processes and solid international business models. The principles are as follows: Each remanufactured component retains at least the same functionality as the original component. Every remanufactured component carries the same warranty as a new component. It is labeled as a remanufactured component and the remanufacturer is identified.
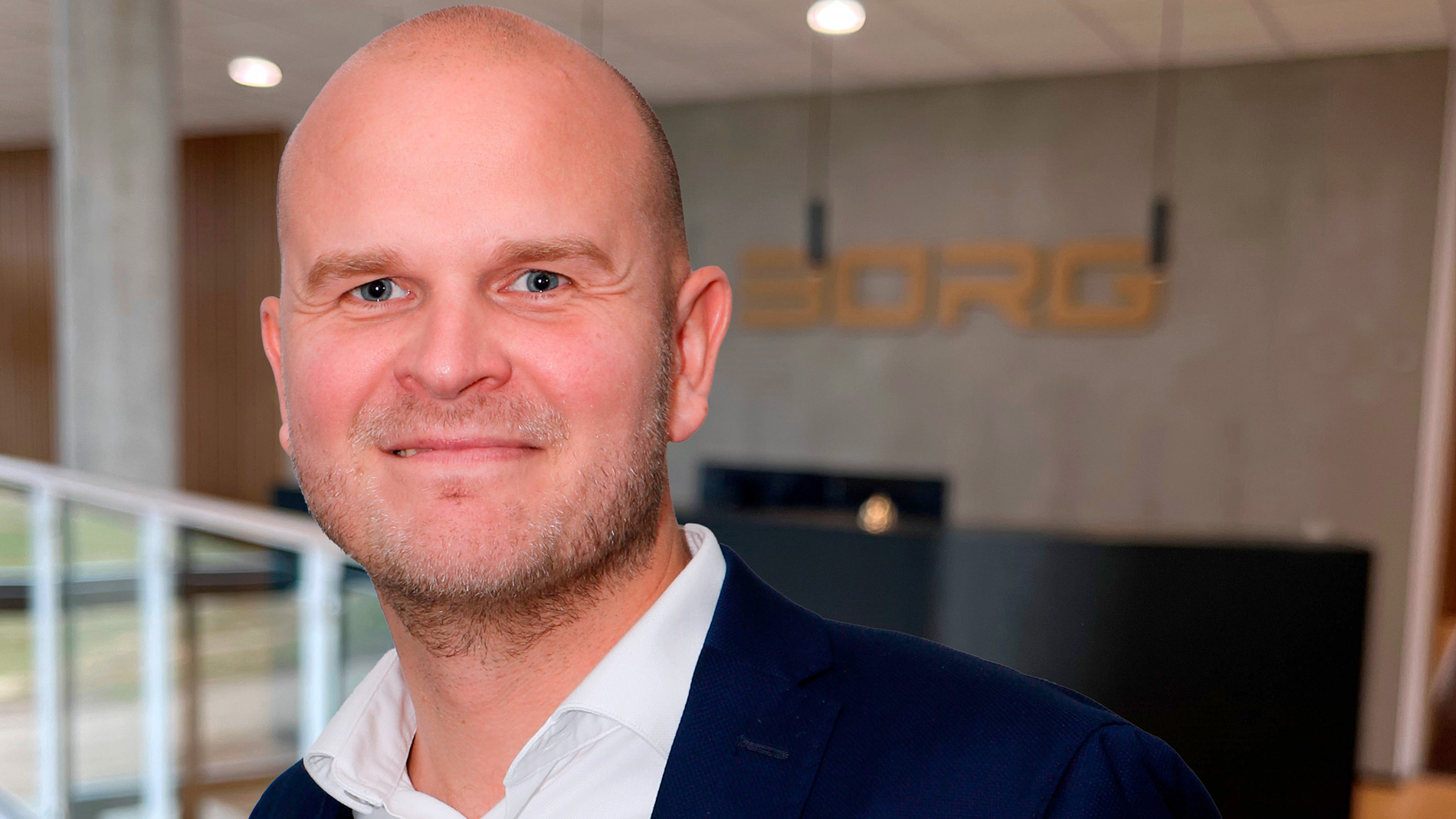
‘At BORG Automotive Reman, we sell our remanufactured units with a deposit, which is refunded when customers return their replaced units to us’, states Kasper Thomsen, CCO of BORG Automotive A/S in Silkeborg, Denmark. ‘We have implemented a return logistics system that efficiently serves our customers throughout Europe.’
In order to have enough parts in circulation, an international network is essential in this market. Thomsen: ‘In order to expand our business, we constantly have to buy in old units, or “cores”, from a network of over 200 active core suppliers, including dismantlers, repair shops and wholesalers. More than 98 percent of our cores are sourced in Europe, which enhances our resilience to logistical challenges from Asia.’
‘At BORG Automotive Reman, we remanufacture starters, alternators, AC compressors, turbochargers, brake calipers, EGR valves, steering racks and steering pumps’, explains Thomsen. ‘We also have a selection of electrical components that we remanufacture. The majority of materials can be remanufactured. According to our Life Cycle Assessments (LCAs), 95 percent of the material weight in a starter, for example, is reused. Wearing parts, such as rubbers, degrade and are therefore not suitable for remanufacturing; they are always replaced.’ From the perspective of a circular economy, the use of such materials should be avoided right from the initial design plans.
‘According to our Life Cycle Assessments (LCAs), 95 percent of the material weight in a starter, for example, is reused.’
Kasper Thomsen, Chief Commercial Officer, BORG Automotive Group
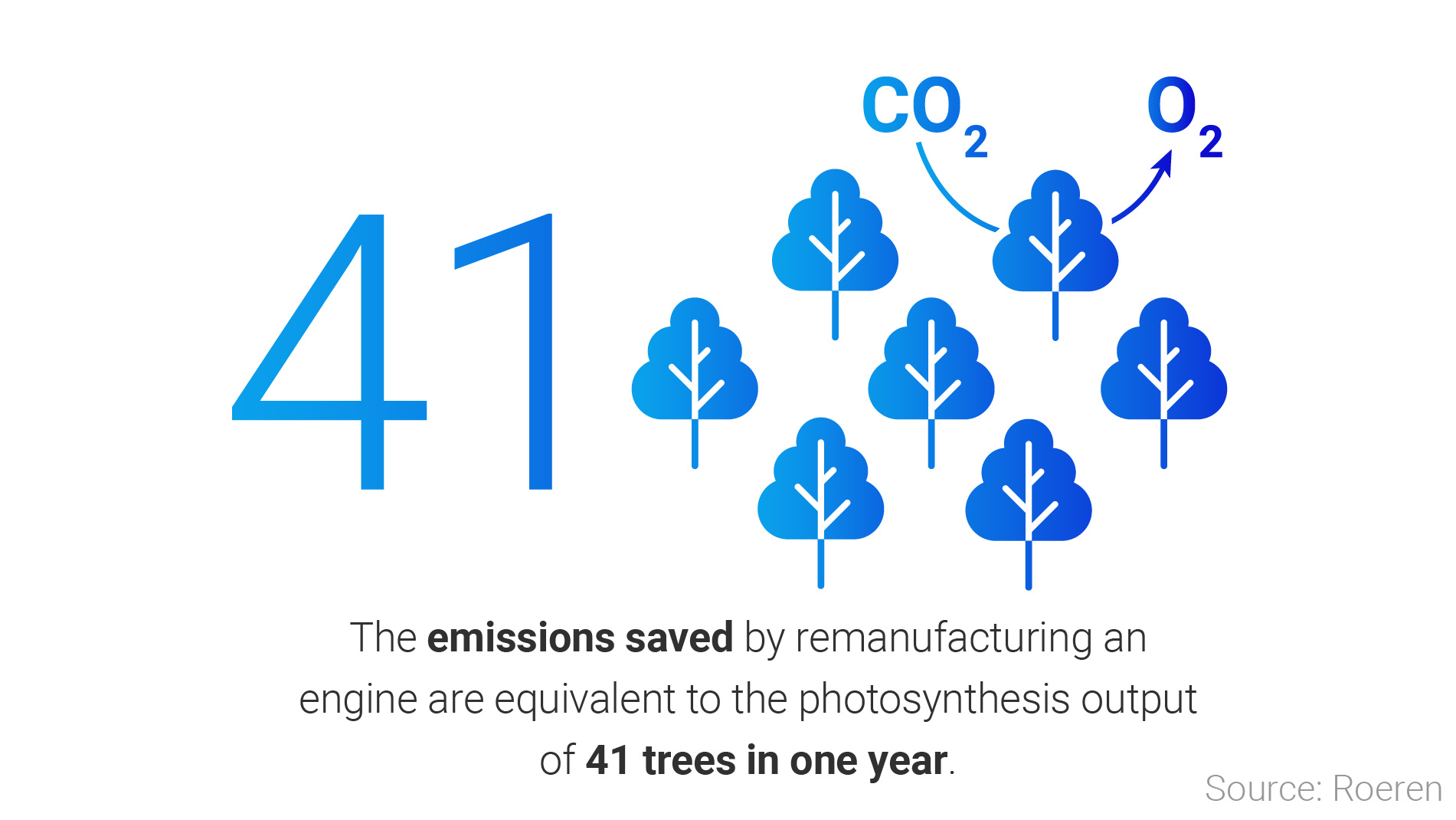
‘Remanufacturing makes a significant contribution to a circular economy’, says Thomsen, ‘in which as much material as possible is given a new life and as little as possible is wasted.’ BORG publishes the life cycle assessments for its eight Reman product groups online. Thomsen: ‘In 2023 alone, our circular efforts resulted in 39,822 tons of CO2 savings, representing a 74 percent reduction in CO2 emissions compared to the production of new parts. Additionally, energy consumption (MJ) is 42 percent lower on average and natural resource consumption (Sb-eq) is 70 percent lower.’
However, circular economy does not just mean using recycled materials or remanufactured parts. ‘You must have the courage to tell the OEM that a car can be produced with the soon-to-be-prescribed 25 percent share of recycled parts. Nevertheless, there is also a need to strive for circularity in new vehicles today’, says Stefan Caba. His expertise lies in calculating the emission values of individual components as early as the design phase.
‘Circular economy means thinking in advance about what I can do with each component at the end of its life cycle. The emissions are already determined in the concept phase’, is Caba's credo. An internal combustion engine produces about a quarter of its emissions during production, with the remainder generated by burning fuel. The electric vehicle has a slightly higher CO2 footprint during production but can be operated in an almost climate-neutral way. In terms of time, this means that the longer the vehicle remains in use, the smaller the footprint per kilometer driven.
‘Circular economy means thinking in advance about what I can do with each component at the end of its life cycle. The emissions are already determined in the concept phase.’
Stefan Caba, Head of Innovation Field Sustainable Vehicle Development, EDAG Group
The evaluation of materials is a continuous process of comparing factors such as footprint, costs, weight, but also the type of use. For instance, it may be advantageous to utilize materials that are lighter but costlier over an extended period of use. In the ‘FiberEUse’ project, EDAG developed a modular CFRP (carbon fiber reinforced plastic) lightweight platform that can theoretically be reused over seven vehicle generations. This is because the advantage of ‘lightness’ (even with the poor CO2 balance of the energy-intensive CFRP materials used in production) ‘pays off in the carbon footprint through long-term reuse’.
‘In principle, you have to build cars like airplanes’, says Caba. ‘A car also has a poor carbon footprint because it is scrapped after only 4,000 hours of operation. An airplane does that in a year. A car simply runs far too little for today's lightweight construction.’
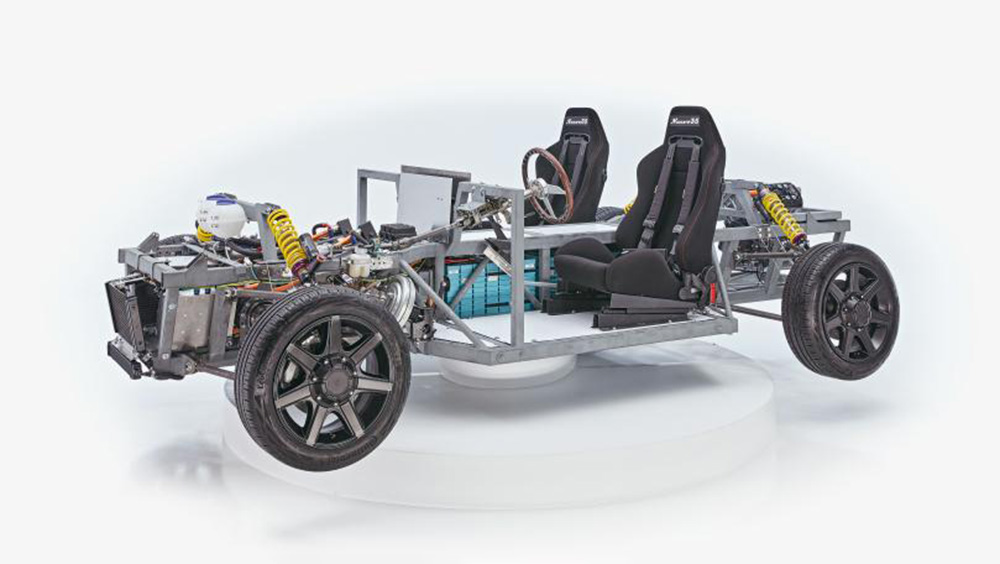
One person who has successfully developed a double zero-emission car is engineer Sascha Dennis-Witte from Dortmund. Together with students from the Dortmund University of Applied Sciences and Arts, he developed the Nuevo 35 prototype, which is an example of clean production and operation. ‘Our primary focus was on achieving the goal, not controlling the costs’, says Witte realistically. The engineer is delighted that the goal has been achieved: ‘Since 2020, the limit in Germany has been 95 grams of CO2 per kilometer for driving alone. The 35 grams of CO2 per kilometer for the Nuevo 35 hybrid, on the other hand, refers to the entire life cycle, including the production of the vehicle, electricity and fuel, and disposal.’
‘The hybrid battery does not require any rare earths’, says Witte proudly. And instead of the primary materials aluminum and steel, which typically have a less favorable environmental impact, the Nuevo uses a new, eco-friendly steel developed in collaboration with Thyssen Krupp. According to Thyssen, this would only result in a 57 euro increase in the cost of an electric vehicle, while significantly enhancing its carbon footprint. Off to Frankfurt! You can test drive the Nuevo 35 at Automechanika 2024.
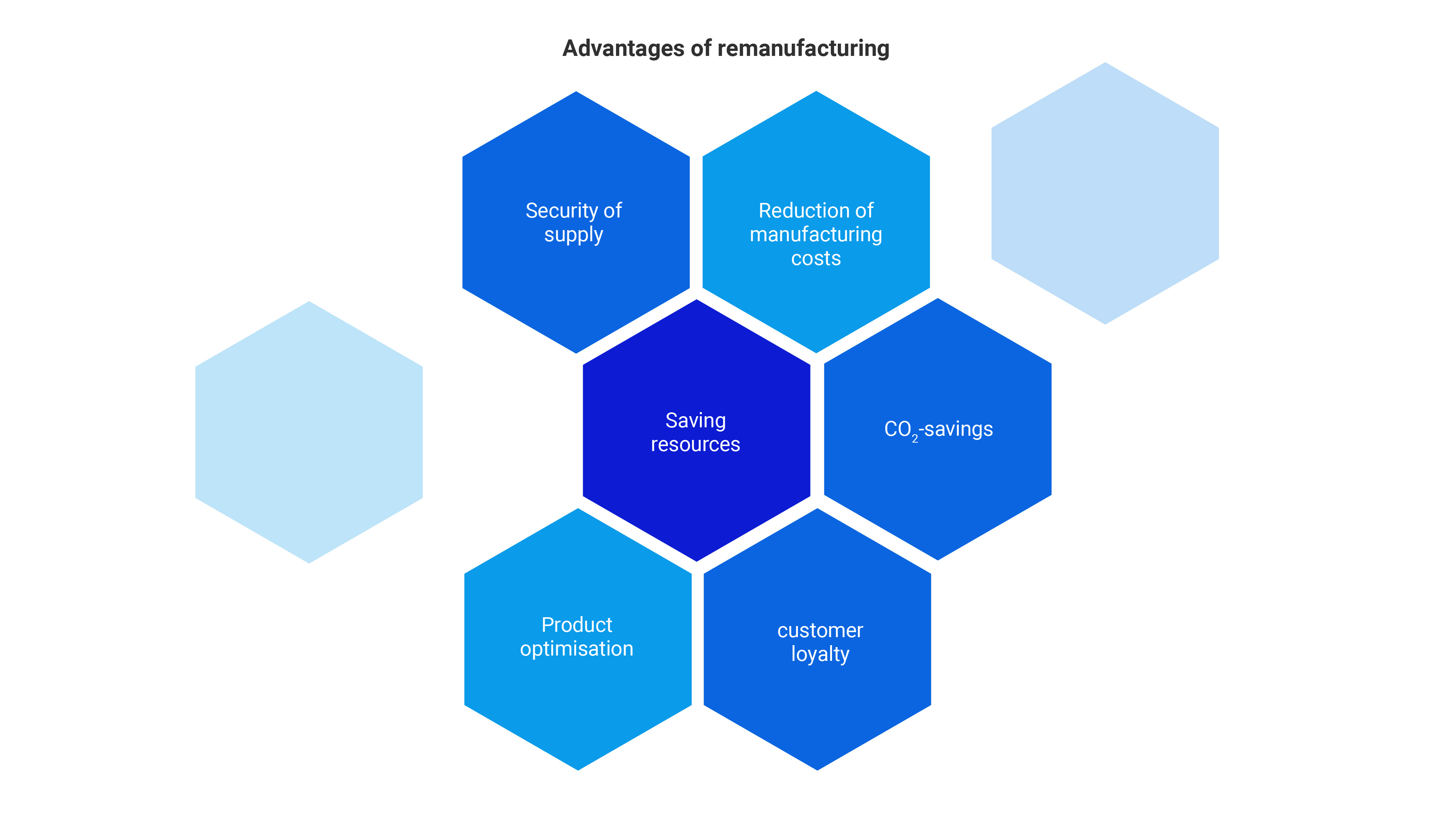
Key qualifications for future engineers
By Luca Cibrario
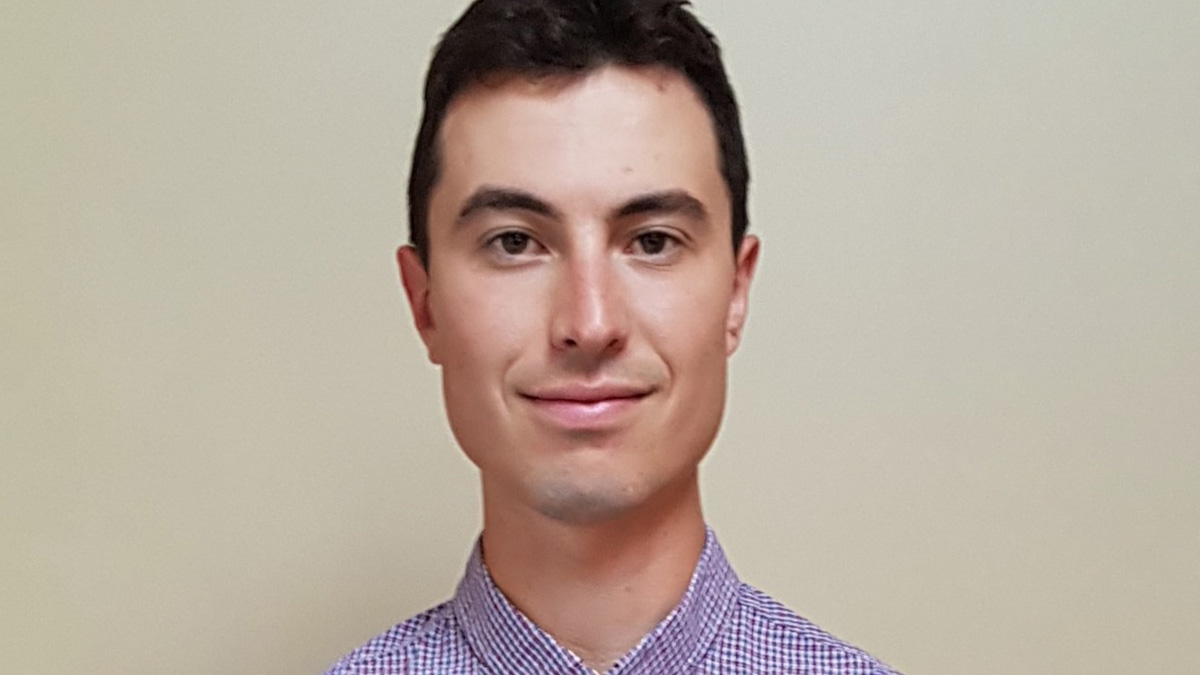
The transition to a circular economy requires a great deal of expertise—and a new way of thinking that transcends traditional boundaries. Based on his experience at the Politecnico di Torino in Turin, Luca Cibrario summarizes the focus that needs to be placed on the training of future specialists.
The engineers of the future need:
- Sustainability skills: an understanding of the principles of sustainability and their application in the design, manufacture and life cycle management of products.
- Systems thinking: the ability to approach problems holistically, taking into account the environmental, economic and social impacts of engineering decisions.
- Innovation and adaptability: knowledge of emerging technologies such as AI, robotics and materials science, combined with the flexibility to adapt to rapidly changing industry needs.