Reading time: 14 minutes
Benjamin Sebrantke, Foliatec
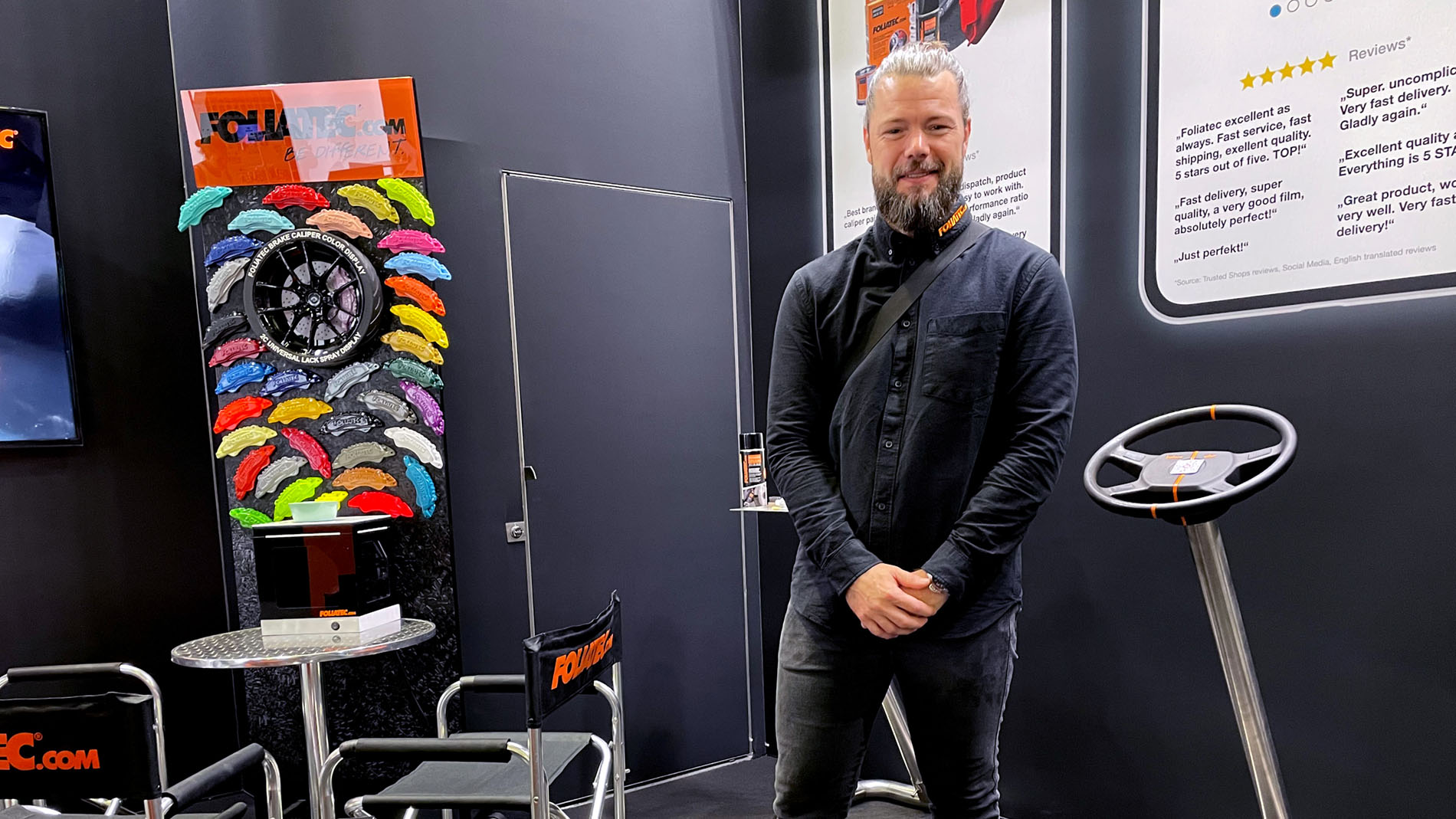
Founded in 1982, Nuremberg-based Foliatec could almost be called a “traditional” company in the highly competitive and fast-moving market for car tuning and car styling products. Its innovative, original and iconic product ideas, combined with high-tech intelligence in the materials and high usability of the products, are probably the reasons for the success of the 40 employees. Foliatec doesn't snooze on trends, sells online and turns every customer into a fan who shares their knowledge on everything from colouring brake calipers to the correct application of spray films in blogs and tutorials – everything you need to know to bring your car up to date in terms of styling and tuning. Everything that can be done with films (safety films, anti-glare films, tinting films) is the main business of the Nuremberg-based company – and now Benjamin Sebrantke, Head of Sales at Foliatec, is moving on to the second megatrend of our time alongside digitalisation, namely climate protection. In this context, the company is developing products for the automotive industry in line with the e-mobility trend. “A new addition to the range is an automotive glass film with a nanoceramic coating that is particularly suitable for electric vehicles”, says Sebrantke. “The film reduces heat build-up in the interior by 95 per cent.” The air conditioning can be dimmed down – and the charge lasts a lot longer. So while tuning is usually ‘hot’ – in this case it definitely is cool.
Guido Hommel, ClimAir Car Comfort
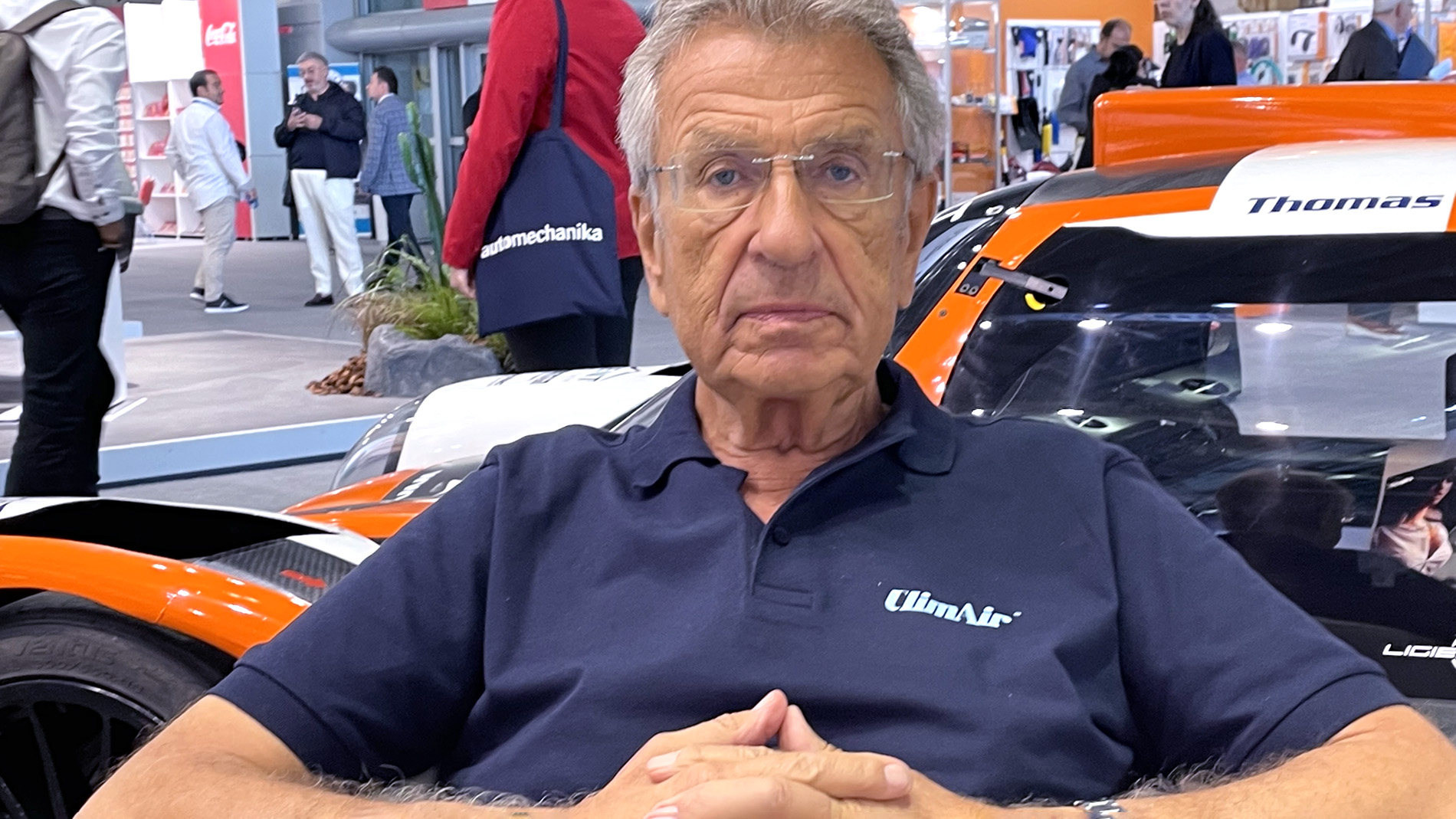
Things have always gone well for Guido Hommel, 81, and there is a reason for that. He sits contentedly at the stand of his company ClimAir, unperturbed by the hustle and bustle of the trade fair. “I've been doing this for so long”, he says, “you gain a certain confidence in what you do.” Starting out as a one-man business more than 50 years ago, the trained plastics fitter (the first at the time) quickly became the world leader in rain and wind deflectors – a position he still holds today. The company’s first product, launched in 1970, was the console of the VW Beetle, a product that would become a historic success. And the future of the company is also assured: based in Karben-Okarben, Hesse and employing 100 people, it will be taken over by one of Hommel’s two children. Hommel is a perfect example of a central element of the automotive supply industry and a major contributor to Germany's status as a leading business location: the SMEs, small and medium-sized, owner-managed or family-run companies whose reputation is often inversely proportional to their success.
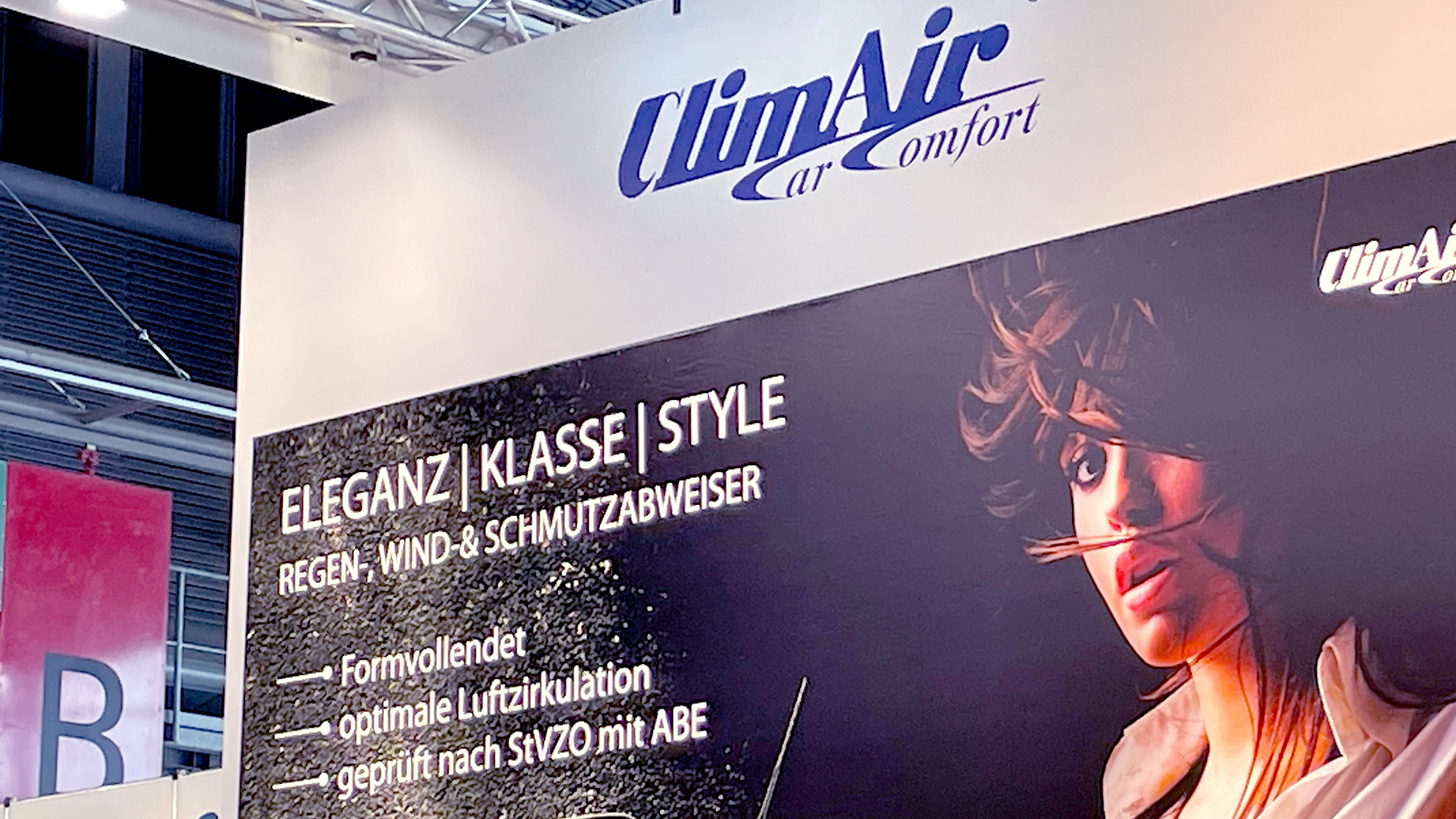
“Speed and flexibility have always been our strengths”, states Guido Hommel. “I never had to ask anyone first when I had an idea.” And Guido Hommel had plenty of ideas – for 18 patents that he holds today. In addition to the rain and wind deflectors launched on the market in 1974, these include the development of the sleeper cab for trucks (1980), spoilers for trucks, the “Sonniboy” sunshade produced in-house in Osnabrück, a rear and loading sill protector, and above all the steady expansion of international business, which has helped ClimAir products from Karben-Okarben to achieve international recognition. ClimAir products are installed in more than 2,400 models from over 80 car brands.
Arash Yazdan, Composite Edge
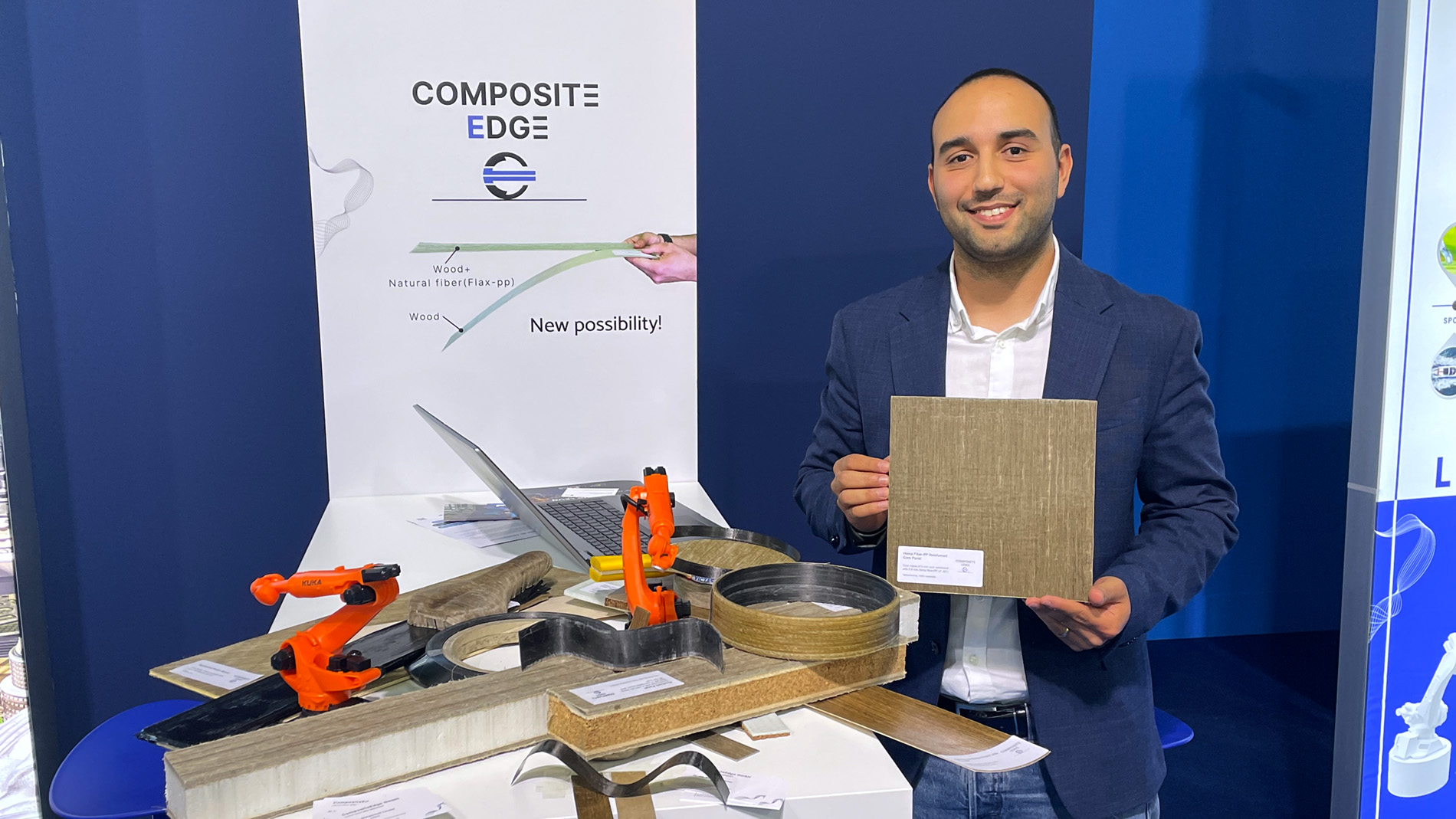
Sustainability and low weight – it’s a match! In the mobility sector, reducing weight is a well-established method for reducing fuel consumption and emissions. Carbon fibre was previously regarded as the optimal solution, but the increasing demands placed on materials in terms of the energy required for their manufacture and their recyclability have prompted a rethink. This is because the total consumption required to manufacture the vehicle is included in the footprint, not just the consumption during use. In this respect, carbon is not the most efficient material. Production is energy-intensive, harmful to health, generates a lot of waste - and the components are difficult to recycle because the bond between the carbon fibre and the plastic in which it is embedded is virtually insoluble. “Especially now”, says Arash Yazdan, one of Composite Edge's three partners, modestly, “when emissions have to be reduced, we see a huge demand – in fact, wherever lightweight construction is required.” With a sustainable composite material that seamlessly combines natural fibres such as hemp and flax with wood, metal, cork, and foams without the use of adhesives, the three-man Braunschweig-based start-up Composite Edge has a real asset. The composite edge material has been developed to achieve optimum strength, and can still be recycled by being chopped. The three developers who took part in the start-up pitch at Automechanika 2024 received one million euros in funding. This will grant them two more years of research and development – and many big customers!
Michael Donath, Elaris
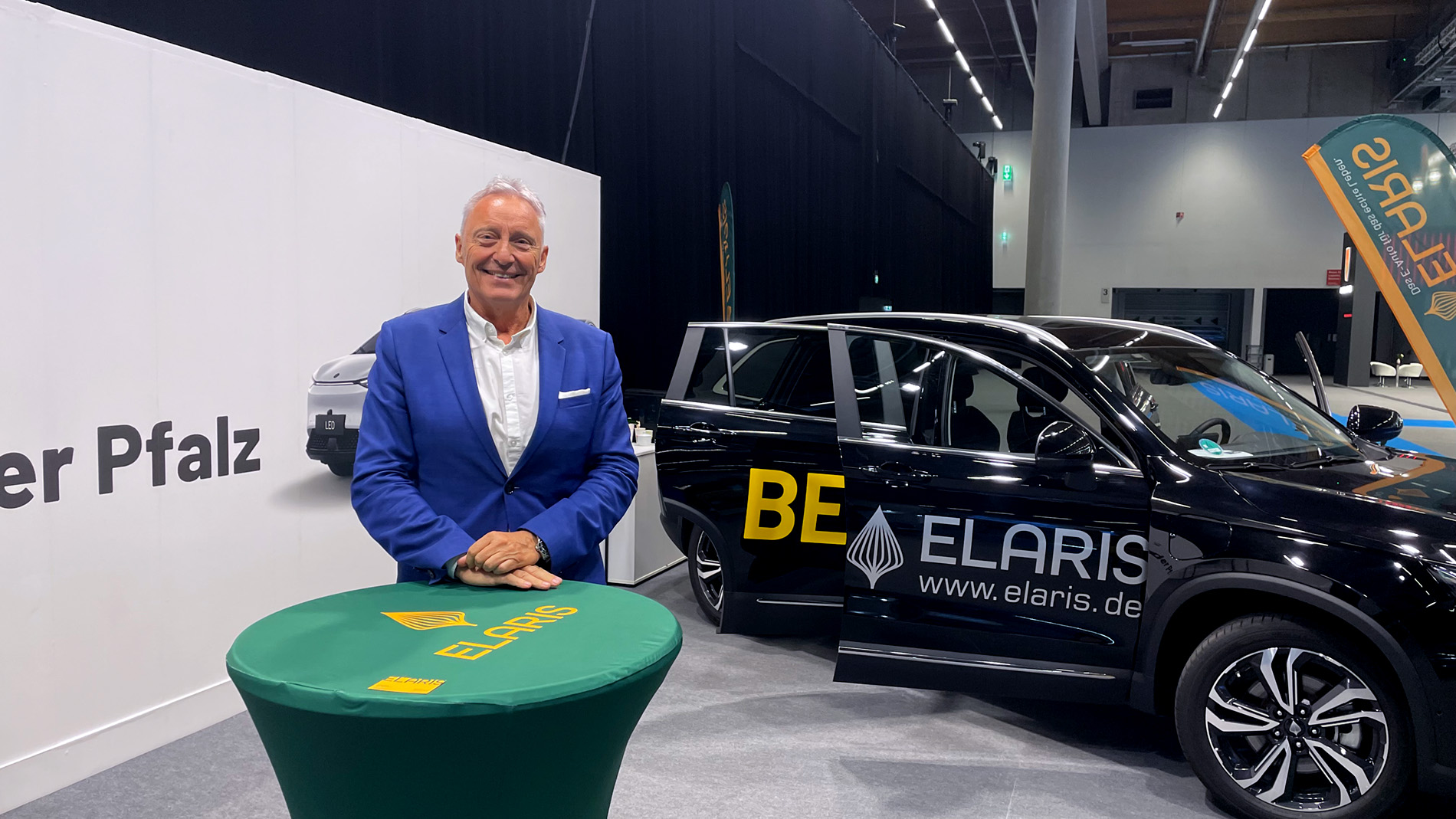
An electric vehicle made in Germany and a new brand? You’re taking on a lot!
Ideed, yes… we are a German automotive brand based in Bad Dürkheim. Our vehicles are produced in China according to our specifications, while our software is developed in Bad Dürkheim.
Who are your partners in China?
Only private companies that are not state-supported and that also produce for the Chinese market. Skywell in Nanjing, for example. The customer only cares about the product and the price, but to us it was important not to become interdependent.
What distinguishes your car, for example the SUV “Beo”, from Chinese products?
This model is not currently available in China. This is due to the fact that the standards and safety regulations in Europe are completely different. We work in a similar way to Apple with the iPhone – Apple does the software and hardware selection, Chinese manufacturers do the production.
What is your company like?
We are currently a team of 40 people and we won’t pass the 100 mark. We are funded by private investors. We try to keep as few areas ‘in-house’ as possible. We are now also planning to set up a final assembly line in Turkey, in a partnership, financed by the cars we sell.
What is your founding story?
We have been in production for two years, with the “Beo” model launched last year. In 2020, our founder, Lars Stevens, had already set himself the goal of offering affordable electric mobility. However, the outbreak of the coronavirus led to a halt in our operations. Lars Stevenson knows China very well – a large part of his family comes from Asia. Our founder is also a senator at the BWA, the Federal Association for Economic Development and Foreign Trade.
What do you see as your market in Germany?
First of all, there will be more cars on the market in 2025 and we are expanding our portfolio. This will also make us more attractive to dealers. Currently, there is a lot of hesitation in the electric vehicles market in Germany.
Sales should be done online and dealers should order online. The Chinese cars in Germany don't intimidate me. They come from China, we come from Germany – people are more likely to open the door for us here. And our quality is excellent. When I started at Elaris, I was surprised by the high standard of our products. Nothing squeaks, there's no plastic, there's a big display, everything is state of the art. We have no reason to hide.
And in terms of price?
I don’t know the cost of Chinese cars in Germany. However, if we consider the equivalent petrol models, we can see that we are approximately 20,000 to 30,000 euros cheaper. This could be an attractive option for companies looking to electrify their fleets.
Mehmet Ali Erdogan, Global CMO Sampa Group
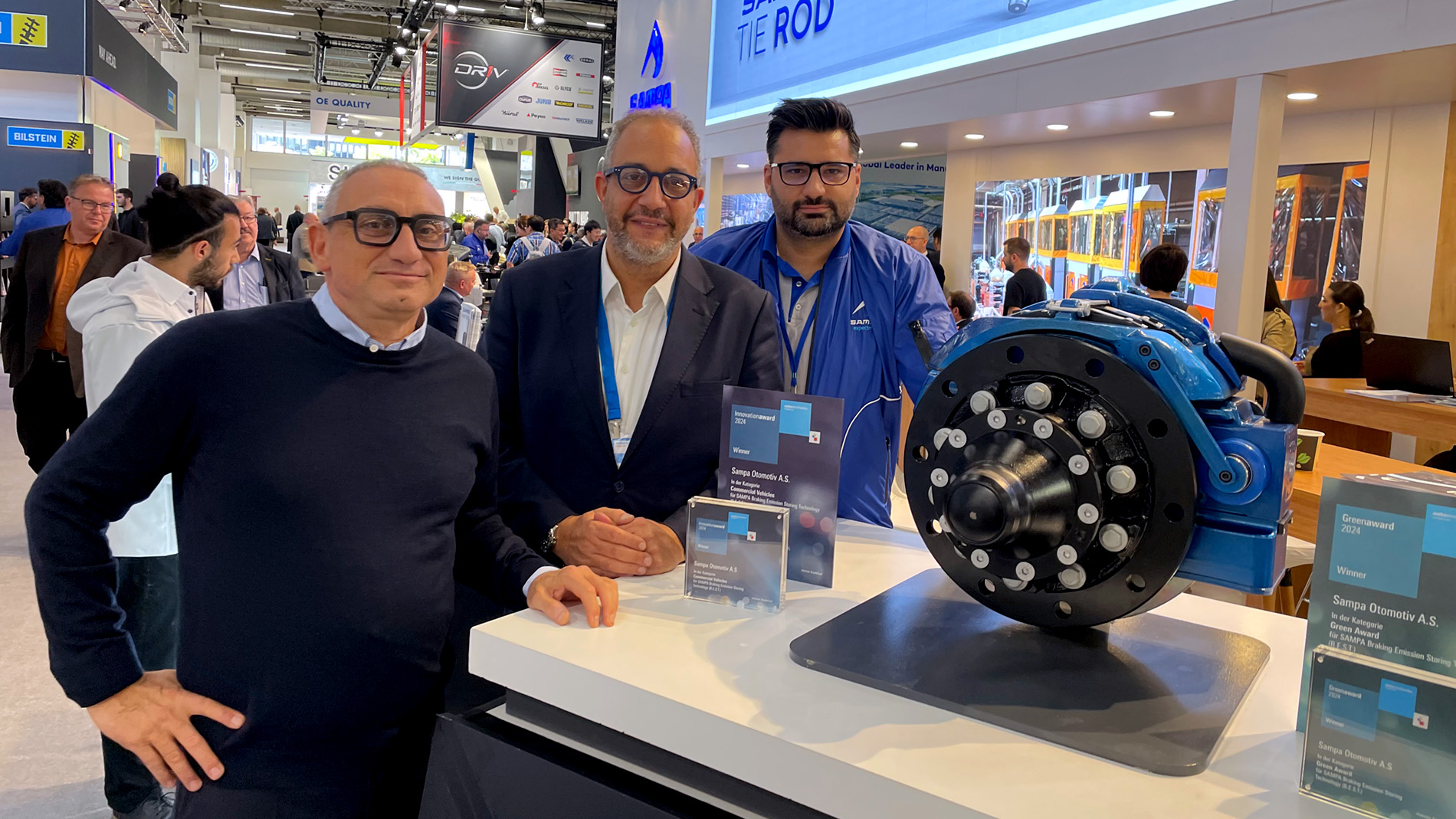
This Turkish supplier won an Automechanika Innovation Award in the “Commercial Vehicles” category for its “Sampa Braking Emission Storing Technology”. This brake filter captures brake pad dust particles at the point of generation, preventing them from being released into the environment as pollutants.
What does the award mean to you?
Mehmet Ali Erdogan: The Automechanika Innovation Award is a great honour for us. But it's not just about this product. We are a sustainable company in general; we have our own department that monitors this. We comply with European directives in everything we do. These days, you have to be aware of what is happening in the world – and make a contribution.
What does it mean to be a Turkish company in this market?
Erdem Sahinkaya: We are a Turkish company, but we are also a global company. What we produce is universal and can be used anywhere in the world. That's why we are in the same league as any European or American company.
What are the conditions in Turkey for running such a company?
Utku Albayrak: We are not the US, but we are not China either. What we lack is an ecosystem for industrial development. The government is taking some action, but it's not enough. We need universities and investment, not from the European Union, but from private sources. Europe has many skilled engineers, but there is a shortage of business ideas. The ideas that do exist lack a business mindset.
What does the Turkish manufacturing industry excel in?
Sahinkaya: Classic standard manufacturing. Our company's strengths do not lie in the fields of computers and software. We have a long road ahead of us in this area.
But does that have to be an obstacle? The physical world still exists.
Erdogan: Absolutely. We do a lot of research and are well connected in order to find out what the industry and society really need. And it's not just electric vehicles and batteries. We also need tyres and braking systems...
There is certainly plenty to develop!
Sahinkaya: We have, by the way, the largest development department in the region, with 300 engineers. We are a magnet for talent from across the country and internationally. We work closely with the University of Manchester. We have a global network. Sometimes our department feels like a real university.
Patrik Koller, David Pröschel, Peak Evolution, Schweiz
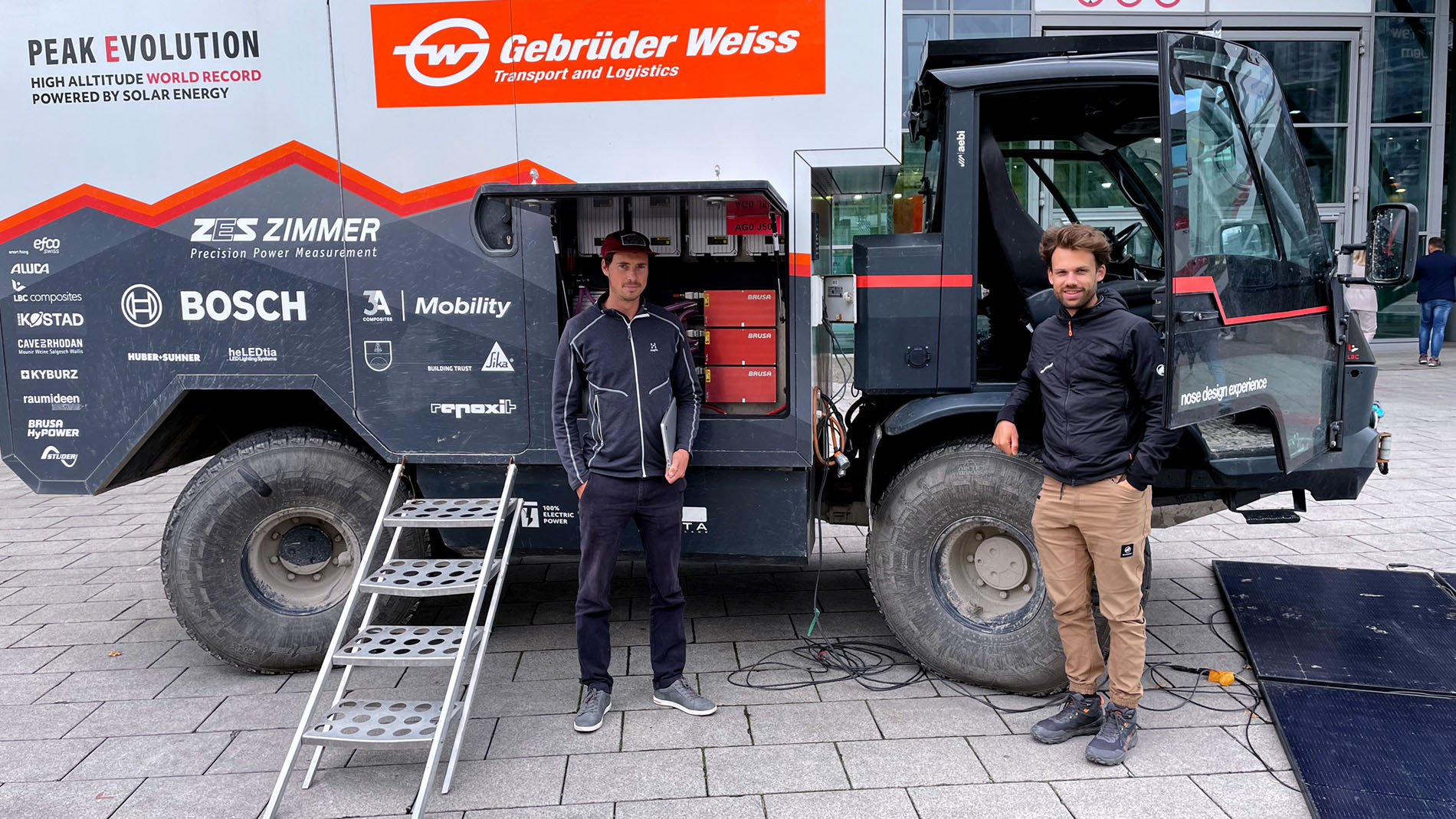
Patrik, David, and David from Switzerland are what you would call great guys. Patrik and one David are brothers, and Patrik was at Automechanika 2024 with the other David. Their “Terren”, a battery-powered electric expedition, off-road and utility vehicle that has now been approved, is parked, a little forlorn, outside Hall 3 at the edge of the Future Mobility Park, but is attracting a lot of interest. Expedition? Yes, because last year the three great guys set the world altitude record for electric vehicles in the “Terren” – over 700 kilometres at 5,950 metres, to the highest volcano in the world, the Ojos del Santo in Chile. Everything about this adventure is real. Completely self-sufficient, with a specially designed solar power system on board (which did fail just once). The expedition lasted three months in total and was accompanied by a professional film crew. The resulting film is currently being funded. And all this to promote a product, namely the “Terren”.
What is the “Terren” as a market development?
Patrik Koller: A fully electric, off-road, multi-purpose transport vehicle for municipal services, ski resorts, agriculture and forestry. We want to electrify off-road transport tasks in local transport. The “Terren” is also interesting for tunnelling and underground mining because it brings less pollution and heat to these construction sites.
What are the other benefits of electrification in these areas?
Electric drive is particularly efficient for multi-purpose vehicles because the vehicles are used a lot uphill and downhill with heavy loads, and recuperation is particularly effective when driving downhill. This also increases efficiency compared to diesel vehicles. In addition, the vehicles usually do not travel faster than 40 kilometres per hour. Air resistance plays a smaller role in fuel consumption than in passenger cars.
And the economics?
We don't need to reinvent anything, we can be economical with existing technology. The TCO (total cost of ownership) of an electric multi-purpose vehicle is lower than that of a diesel vehicle.
Florian Heizmann, Gedore + Schaeffler
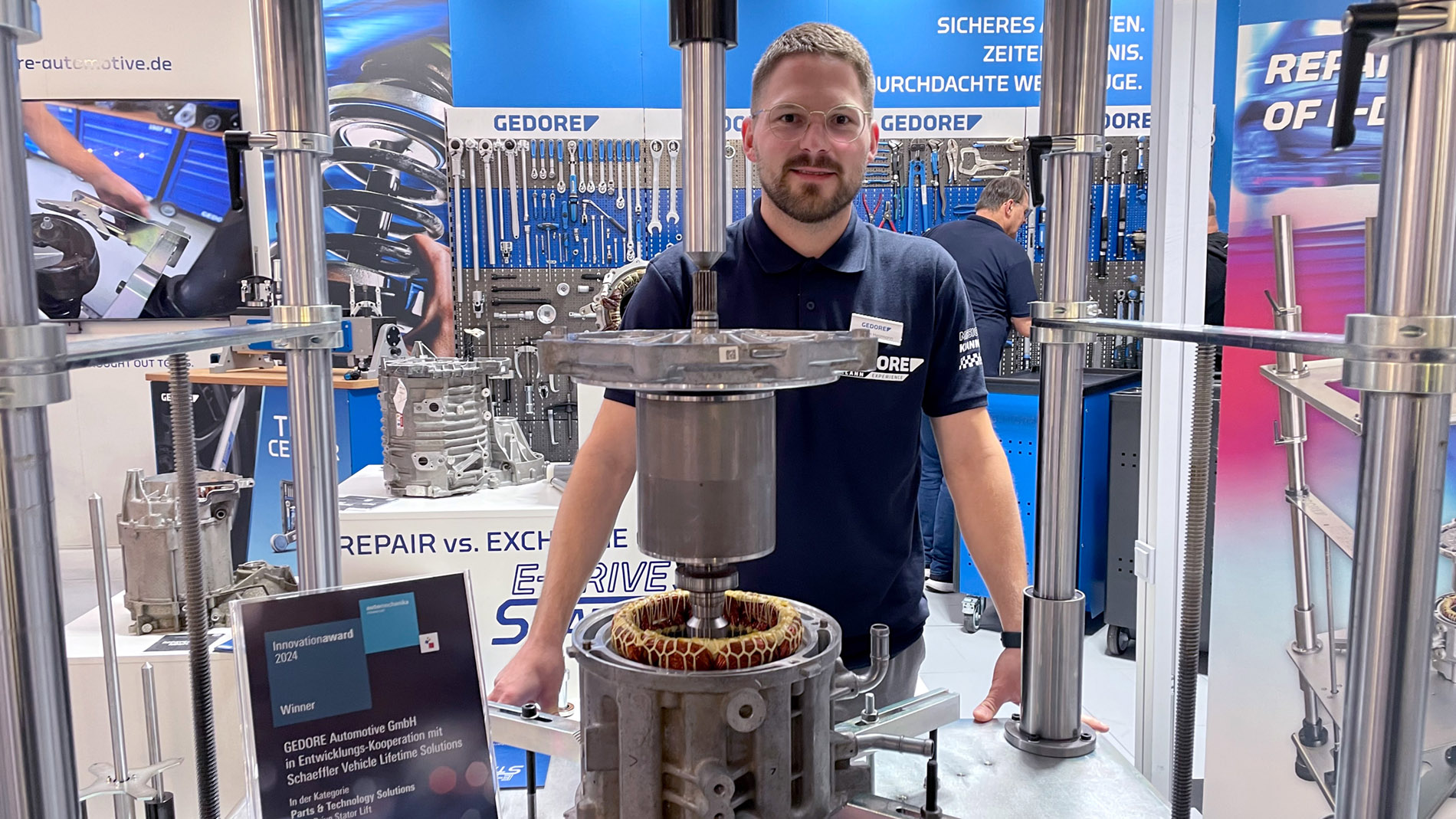
Until now, electric engines have been the wallflowers of the engine world. They have never had the magic of a 12-cylinder internal combustion engine, or even a two-stroke. Which is doing them a disservice. After all, they do their indispensable job billions of times a day in everything from shavers and lawnmowers to high-speed trains – and supposedly they don't break down, they don't smell and they don't make any noise. Perhaps that's why they get so little attention. But what happens when they do break down? It's a question that arises in the context of increasing e-mobility. Until now, most electric motors could not be repaired – and were simply thrown away. The “E-Drive Stator Lift”, another winner of this year's Innovation Award, offers a solution. The device, developed by Gedore Automotive in Donaueschingen in cooperation with Schaeffler Vehicle Lifetime Solutions, is a mechanical device for dismantling automotive electric motors to enable the subsequent replacement of parts. While GEDORE is presenting the E-Drive Stator Lift, Schaeffler is launching customised repair kits on the market. Incidentally, the first discussions about this development took place at Automechanika in 2022. “Due to the extremely high magnetic forces, it was previously impossible to separate the rotor and stator without damaging them”, says Florian Heizmann, a young designer who trained as an automotive mechatronics engineer and then underwent further training to become a state-certified technician in automotive engineering. Once the two elements have been separated, they must not come into contact with each other, as this will damage the lamina stacks. During the “operation”, the rotor is fixed in the highly rigid device between two centring spikes to maintain stability and prevent any wobbling. The “E-Drive Stator Lift” achieves this impressive feat with mechanical precision. After being separated, the motor can be dismantled and the parts replaced. “Throwing away electric motors is simply not good for sustainability”, says Heizmann, describing the problem he has solved. “After all, they contain valuable resources such as rare earths, the extraction of which we should definitely reduce.”
Raimund Brandstätter, Aviloo
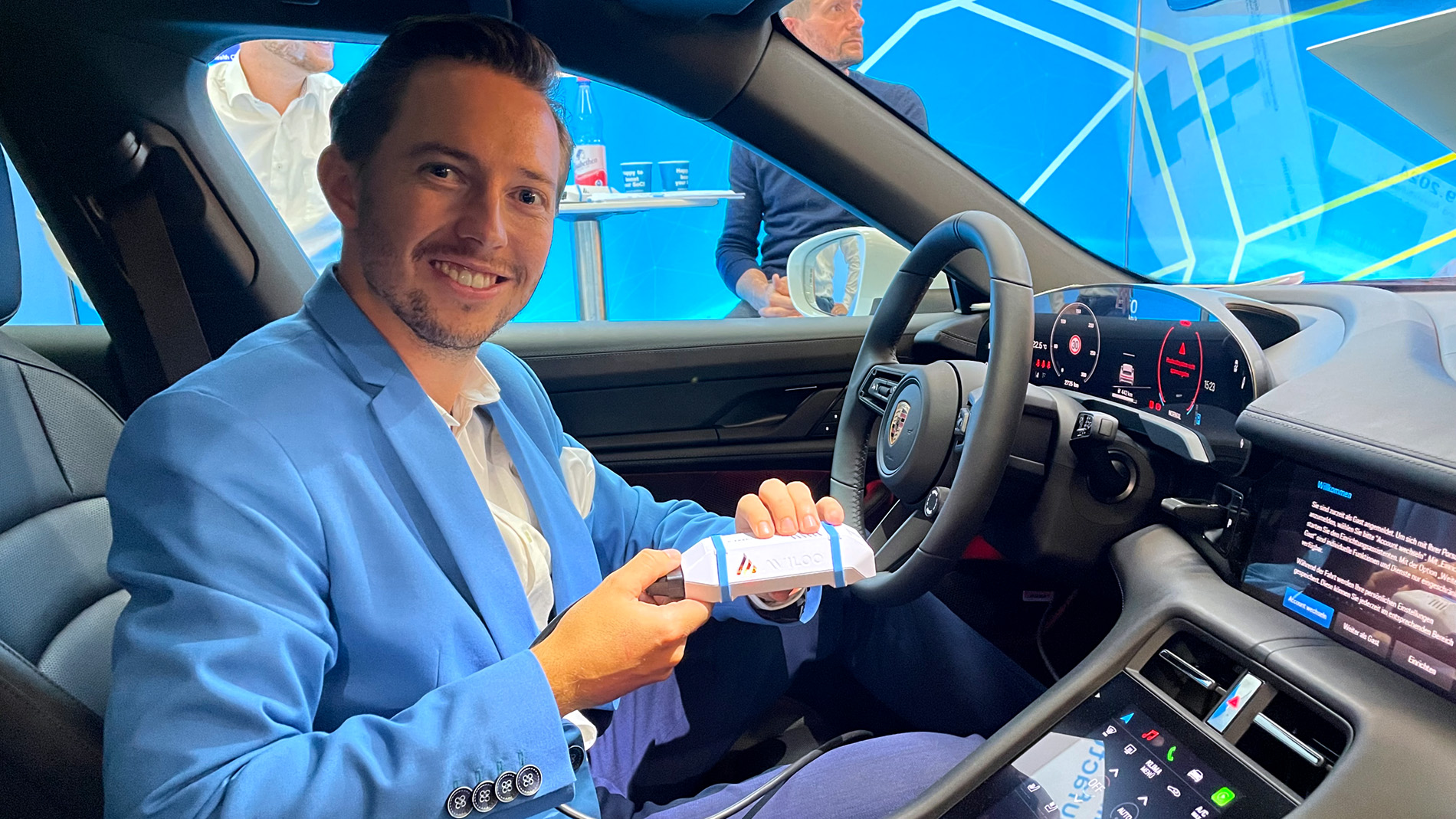
AVILOO, a start-up founded by Wolfgang Berger and Nikolaus Mayerhofer in 2017, has found answers to questions about the condition of batteries when buying used electric vehicles. The resulting software solutions are so groundbreaking for the electric car and plug-in hybrid industry that they received an Innovation Award in the ‘Electromobility & Alternative Drive Solutions’ category in Frankfurt. ‘The founders‘ idea arose from the need to buy a used electric car themselves - and it was not possible to find out how much battery capacity was left in the used car,’ says Raimund Brandstätter, CSO of the company in the south of Vienna, which now has around 50 employees. Knowing the current value of a traction battery is essential for a purchase decision, as this can account for up to 50 per cent of the value of the entire car. The ‘AVILOO FLASH Test’ is a plug-and-play style battery test that checks the functionality of EV traction batteries in just three minutes on a stationary vehicle and presents a comprehensive report including a score. Brandstätter: ‘Our test is manufacturer-independent and covers 95% of all available brands. The test certificate gives buyers certainty about the residual values and actual performance and health of the used e-vehicle's battery.’ The AVILOO FLASH test measures defects down to cell level, temperature fluctuations, the functionality of the battery management system and many other parameters. It is therefore at a level of technology that is ‘unique’, as Brandstätter says, and which makes AVILOO the global market leader. The basis for success: a database that continues to grow with every test. In any case, the AVILOO team has the wonderful feeling that its work is meeting a real need. Online sales platforms for used cars now offer ‘battery certificate’ as a filter when searching.
Continental Tires
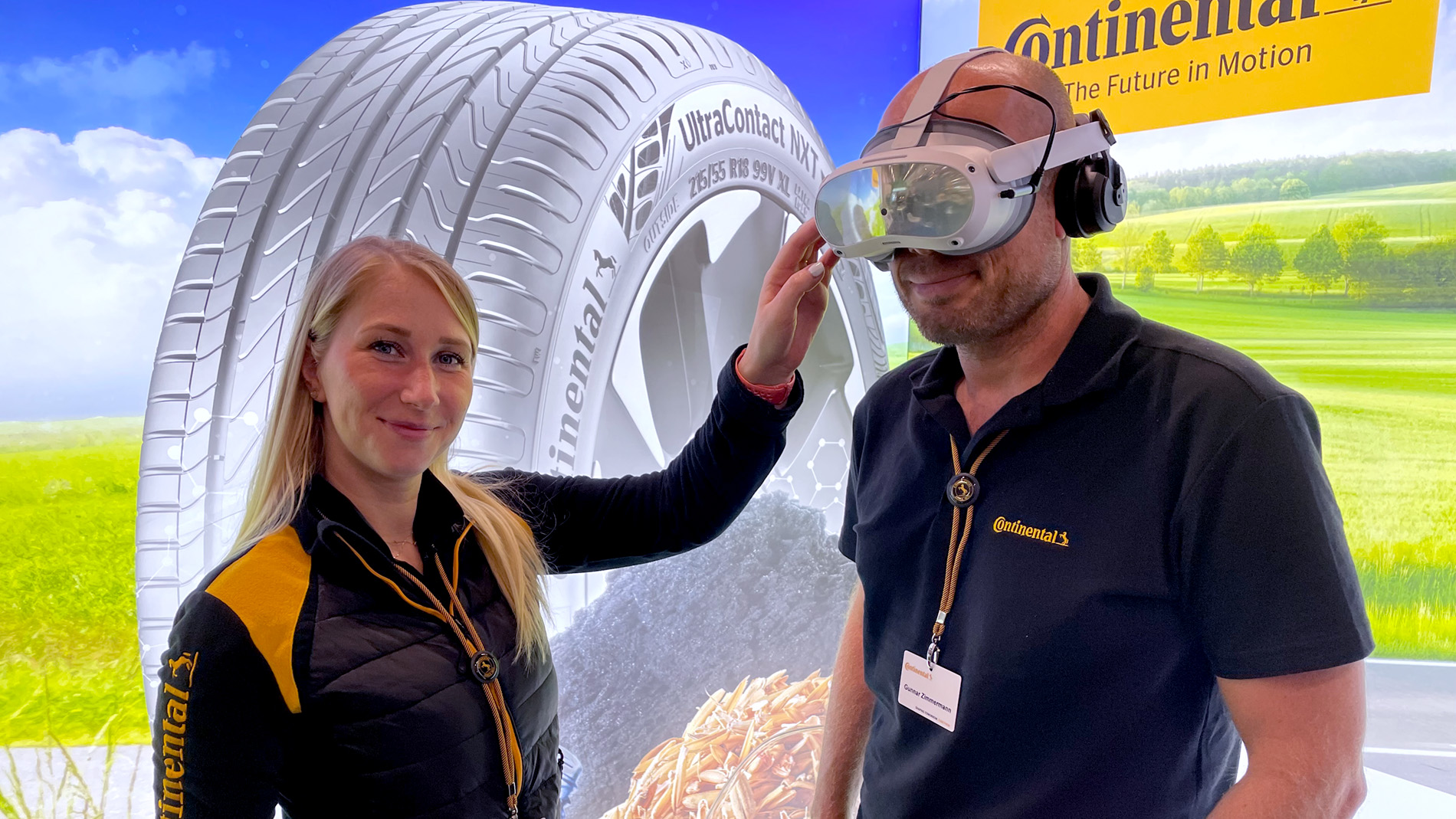
At Automechanika 2024, Continental presented impressive innovations under the motto ‘Shaping Tomorrow. Together!’, Continental presented impressive innovations and sustainable solutions. The stand next to the Sustainability Court stage, where the UltraContact NXT took centre stage, was particularly fascinating. This tyre, one of the most sustainable on the market, consists of up to 65% renewable, recycled and mass balance certified materials and offers maximum safety and performance. The highlight at the stand: VR goggles that allow visitors to experience the sustainable tyre from the Continental portfolio up close. In an interactive VR film, the various sustainable materials such as recycled rubber, PET bottles, recycled steel, bio-based resins and natural rubber could be put into production themselves. It was impressive to see how such high-performance and sustainable tyres are created from these materials. But that wasn't all. With VR goggles in front of your eyes, you could also experience the performance of the UltraContact NXT on a Continental test site. Sitting next to the tyre tester, you drove through the steep bends with excitement and felt the outstanding grip of the tyre. An exciting and up-close experience that gave a deep insight into Continental's innovative strength and commitment to sustainability.
Overall, Continental's presence at Automechanika 2024 was an impressive example of how new technologies and sustainability can go hand in hand to shape the mobility of the future.