Reading time: 5 minutes
1. Production
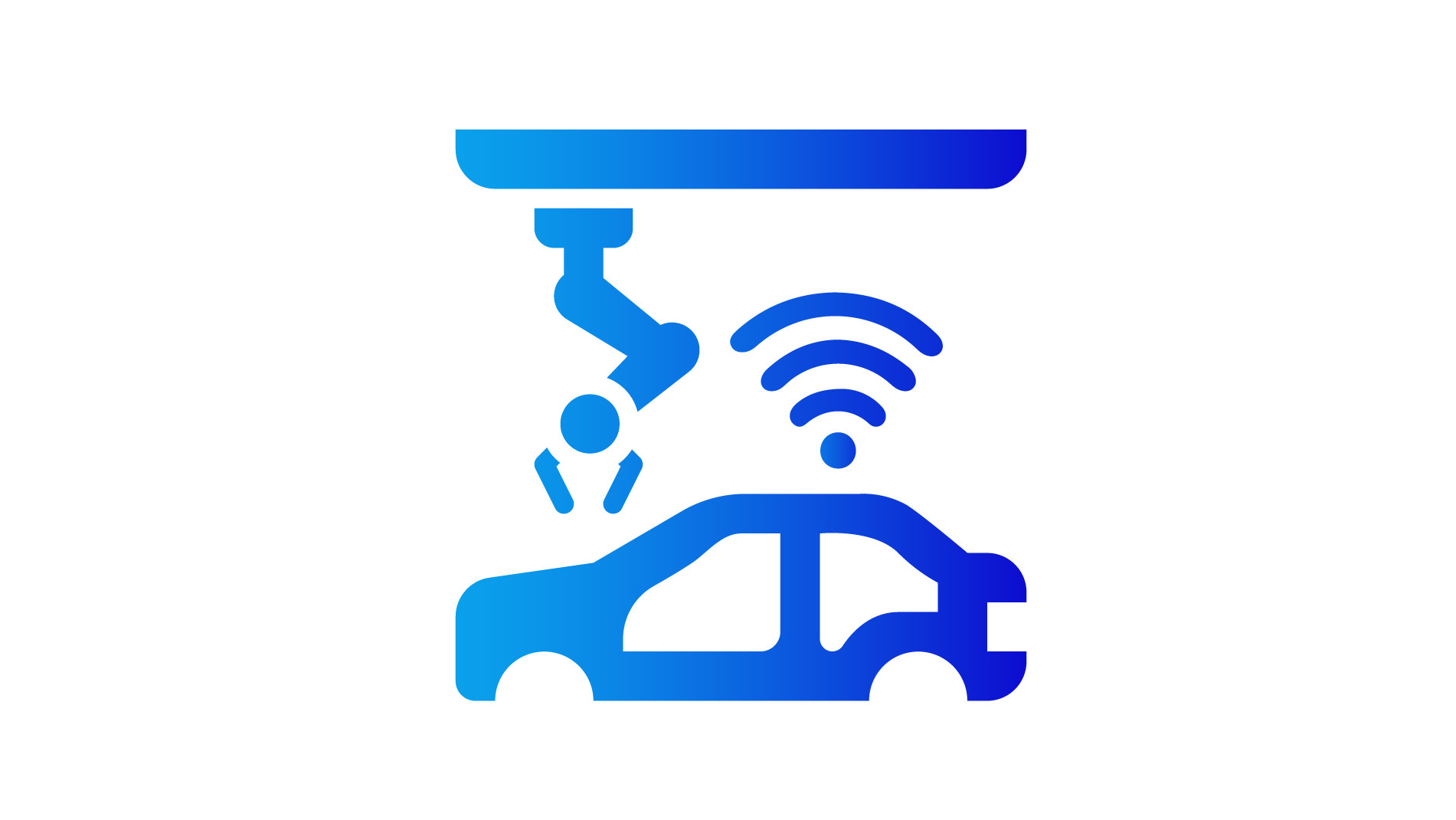
A major factor in building electric cars that are environmentally friendly from the get-go is the extraction of raw materials. Key materials such as lithium, cobalt, and nickel are crucial in keeping the ecological footprint as small as possible. Many manufacturers are investing in recycled materials and looking for alternatives to conflict-ridden raw materials. However, production processes themselves must also be as efficient as possible in order to conserve resources. BMW, for example, relies on the use of digital tools such as data science and artificial intelligence. As a result, the vehicle itself becomes a communicating participant in the production. It provides continuous updates about its production status and reports assembly errors, which it recognises autonomously. In this way, the use of materials and time is optimised and quality standards are improved. This approach has made it possible to continuously reduce CO₂ emissions in recent years.
2. Energy and charging infrastructure
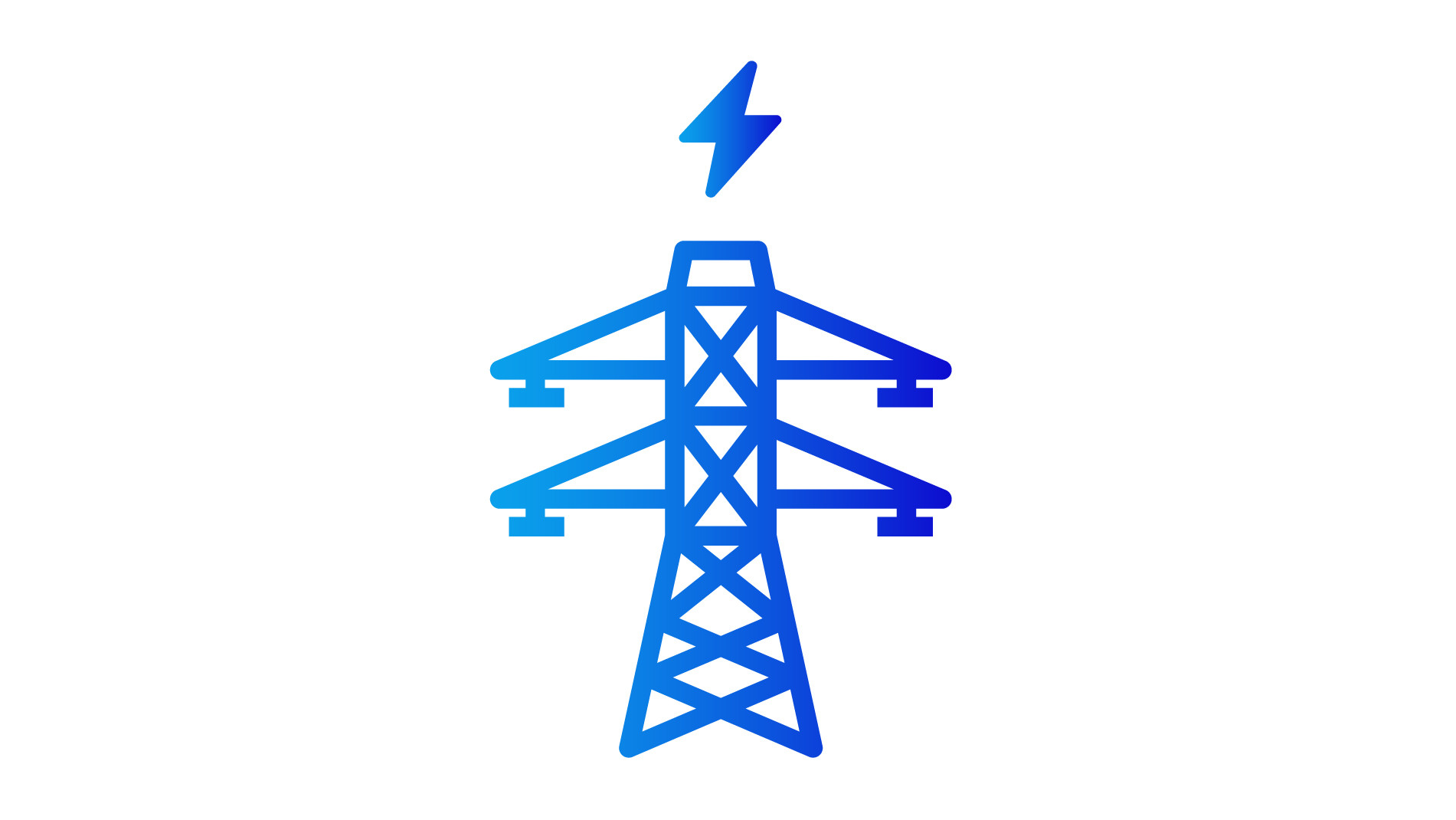
Climate-neutral mobility requires more than cars powered by electricity. It requires a holistic approach in which all components of the electricity and transport sectors are linked. Smart charging is an important keyword here – it describes the use of innovative technologies to set up local distribution grids in a particularly smart way. This is because the future lies in expanding the ability of electricity grids to store energy at some points in the network and release it at others. This requires bidirectional communication between electric cars and the electricity grid. The software that controls the grid management and storage technologies, for example, will be supported by artificial intelligence in the future.
In this way, the electricity and transport sectors will be linked more closely together, in order to ensure a highly efficient use of energy generated from the sun and wind. It will also make it possible to better control the simultaneous mass charging of cars. It also prevents consumption spikes and ensures that the electricity grid and electricity prices remain stable and that charging times remain short.
3. Range and power consumption
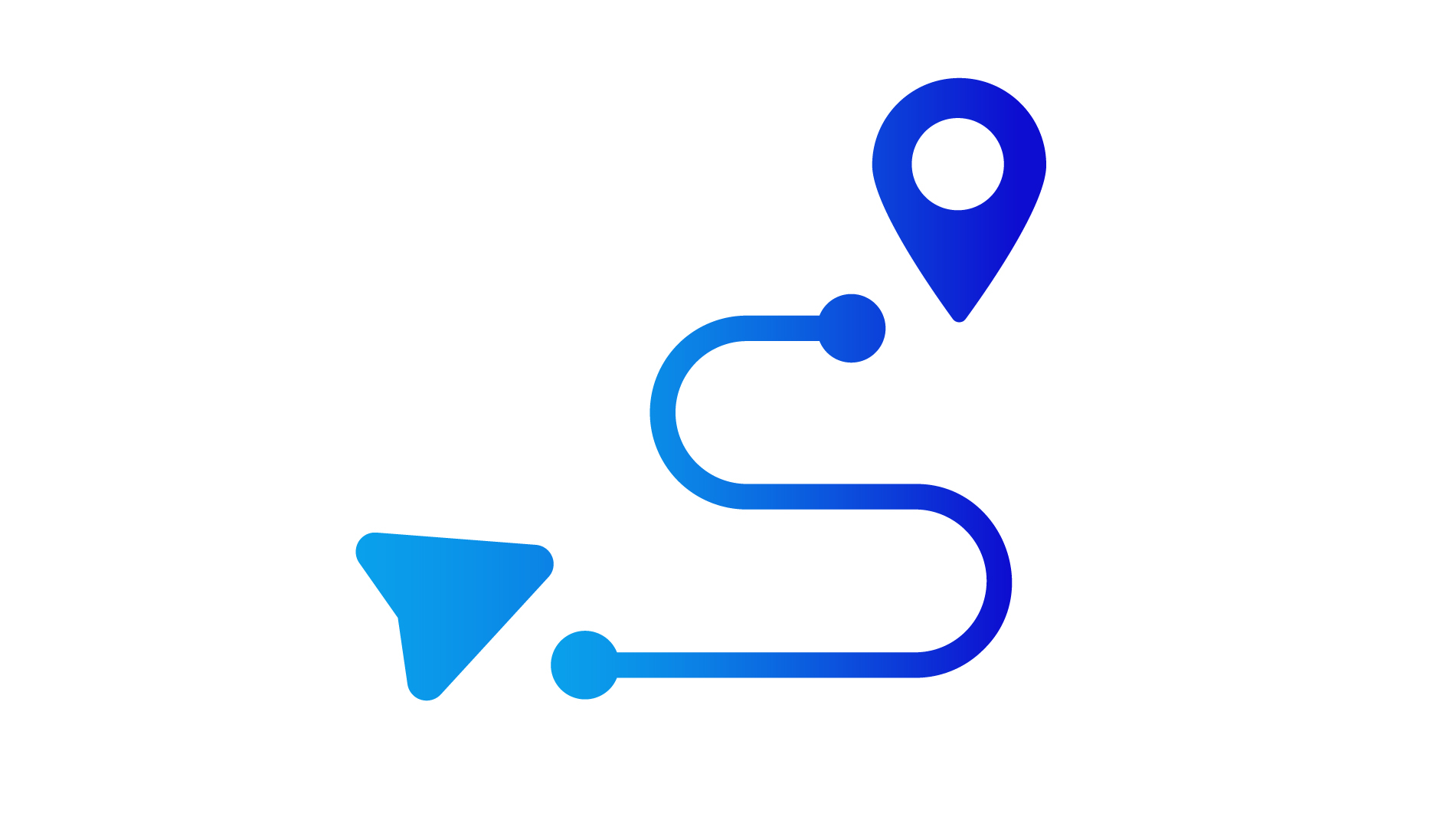
With “Reichweitenangst”, – much like “kindergarten”, “wunderkind” and “poltergeist”, there is now another German word that is catching on in English. Loosely translated as ‘range anxiety’, Reichweitenangst is one thing that may be deterring buyers inside and outside of Germany from switching to electric. However, this ‘angst’ is slowly becoming irrational, as research and industry have made progress beyond all expectations in terms of battery range: While customers had to make do with 90 to 150 kilometres in a lower mid-range car back in 2021, the figure is now 150 to 400 kilometres, and in the mid-range it is already 600 kilometres on average. This should be enough considering the average of 10.9 kilometres that a car travels in the city each day. A holiday trip should also be possible with charging route planning, for which there is a host of digital tools available. Longer ranges with higher consumption - how does this fit in with the goal of climate neutrality and e-mobility? As with combustion cars, manufacturers are making sure that the increase in range is not only achieved by utilising more energy, but also by reducing consumption. (At the moment, the electricity consumption of an e-car for 100 kilometres is around 15 kilowatt hours and therefore around 4.65 euros). The levers for this lie in the efficiency of the drive (motors and electric axle) and the power guzzlers in the electric car, of which the heating and air conditioning are the biggest. According to a study by the VDI, they account for up to a third of consumption, depending on the outside temperature. Heat pumps present an alternative here. They can be retrofitted and –after an investment of 1,000 to 1,500 euros– provide cost- and emission-free air conditioning for the interior in the long term. Another variable –depending on the capability– is the weight of the battery: it ranges between 250 (VW up!) and 700 kilos (Tesla Model S).
4. Drive, power electronics, electric motor
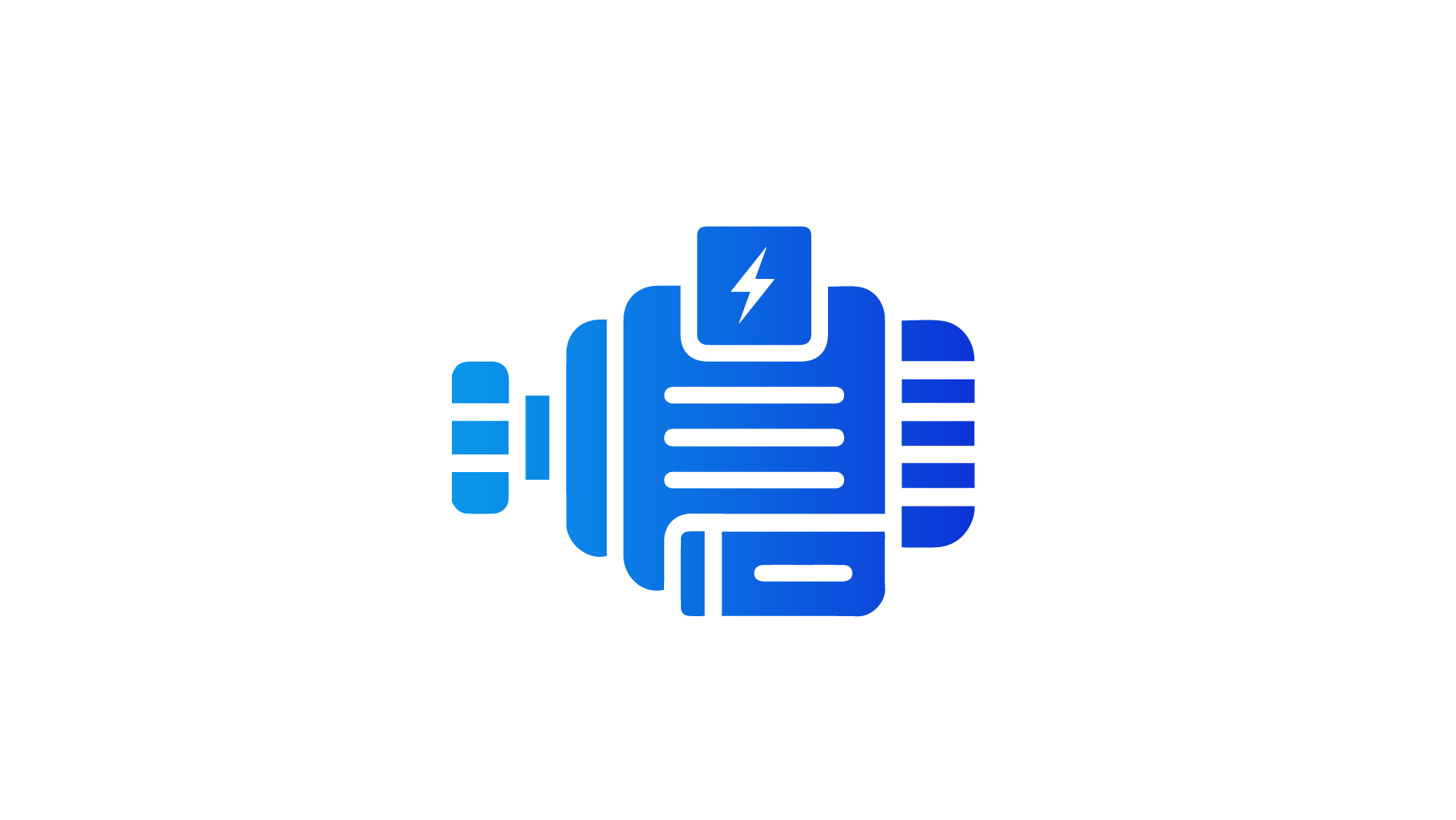
There are three main components of electric cars in particular that need to be further developed in order to increase their performance and efficiency: the electric motor, the power electronics, and the drivetrain. In the case of the electric motor, progress is expected primarily in the dimension of materials, particularly magnets and copper windings, as these increase efficiency and power density. Lightweight, low-loss materials minimise heat development and increase the range. Innovative motor types such as permanent magnet synchronous machines offer high torques and energy efficiency. Optimising the power electronics also promises major benefits, as improved power electronics allow for more precise control of the power supply. Materials such as silicon carbide and gallium nitride increase efficiency as they enable higher switching frequencies and generate less heat. The integration of intelligent controls also optimises the current flow and reduces losses.
And finally, there are also innovations in the drivetrain: Integrated axle drives and lighter materials reduce vehicle weight. By optimising the transmission and axle, the engine power can be transmitted better, which increases acceleration and range.
5. Raw materials and supply chains
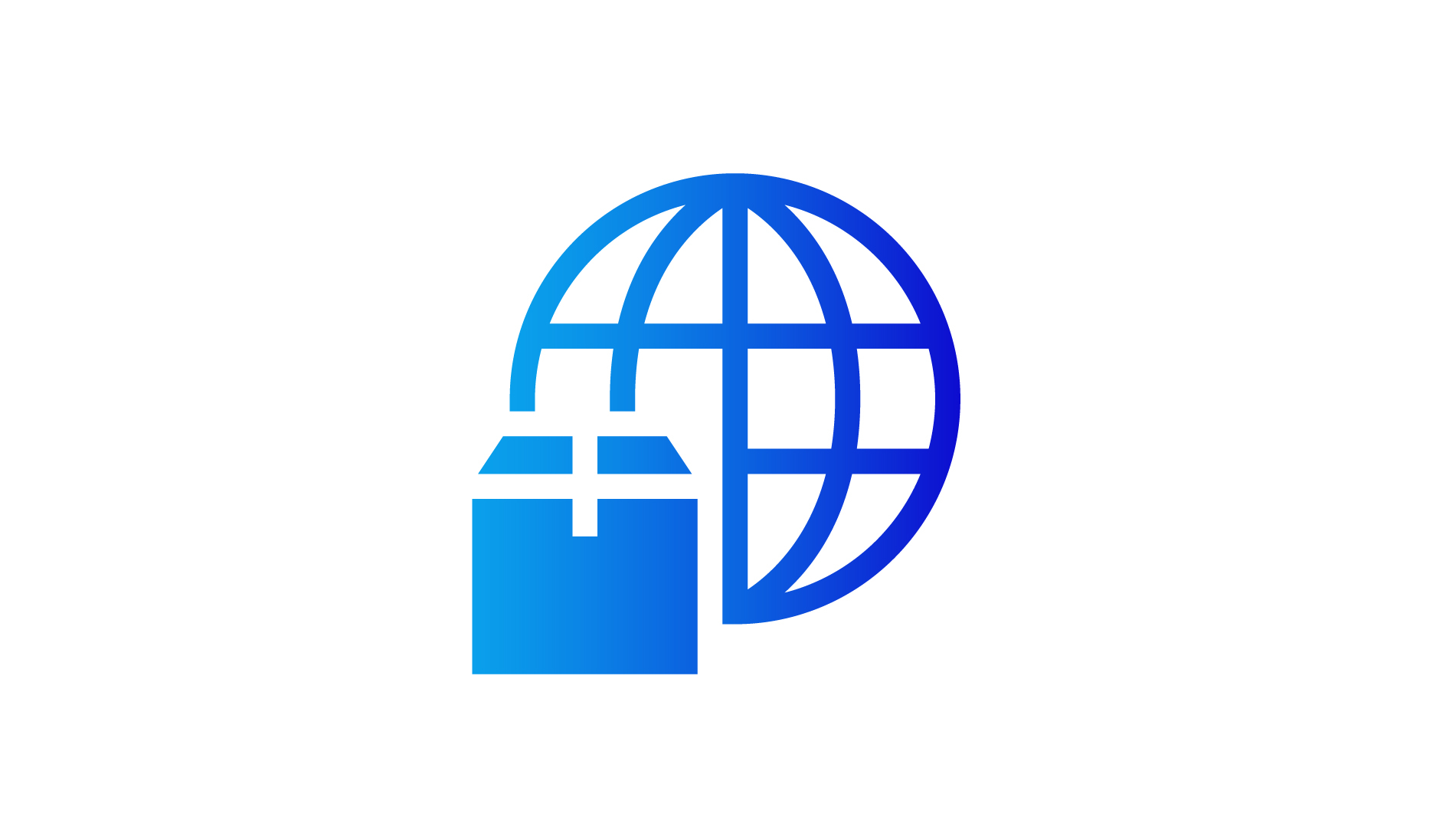
The supply of raw materials is the bottleneck of the energy transition. This is particularly apparent in the electromobility supply chains, as the extraction of critical raw materials such as lithium, copper and cobalt in the countries of the Global South is linked to social and ecological crises. As the proportion of these materials in batteries, for example, can only be reduced slowly, a high recycling rate within circular supply chains is necessary to reduce demand. The situation here, however, is far from ideal: The proportion of recovered lithium from battery recycling worldwide currently accounts for a mere one to two per cent of demand, three to five per cent for nickel and up to nine per cent for cobalt. In a major study, the human rights organisation Amnesty International has evaluated 13 leading electric car manufacturers on the extent to which they pay attention to human rights violations along their supply chains. German car manufacturers such as Mercedes, BMW and VW or Elon Musk's Tesla score comparatively well. Think tanks, consultancies, and university institutes are working feverishly on instruments to help companies reduce their manufacturing footprint. The current imbalance in production capacities makes this difficult. Many European car brands are now produced entirely in China – according to the environmental standards that apply there – and are already trailing heavy ecological baggage by the time they arrive in car dealerships in Europe.
6. Battery recycling
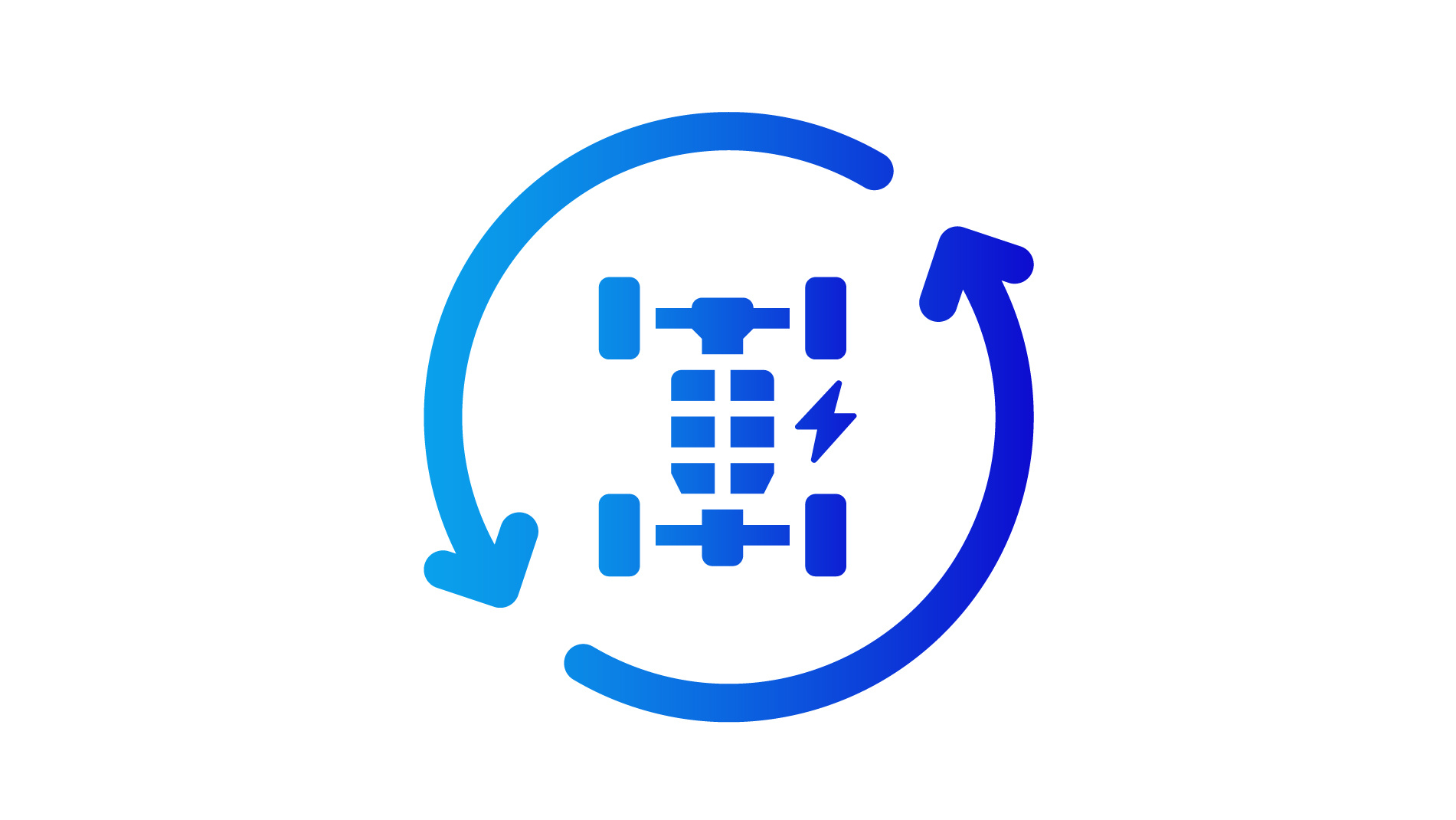
Europe is facing an enormous challenge. With the increasing popularity of e-cars, the recycling of used batteries is becoming an important part of production. In the coming years, Europe can expect a wave of used batteries that need to be disposed of sustainably. In order to reduce the demand for raw materials such as lithium and cobalt, the EU is developing strict recycling requirements and is striving for a circular economy in which used batteries serve as a source of these valuable materials. A look at China shows that Europe has some catching up to do. China has already established comprehensive recycling structures: The country is expecting around 3,000 kilotonnes of batteries to be recycled by 2030 – a huge increase compared to the 294 kilotonnes in 2021. China is relying on strict regulations and economic incentives to promote the recycling and reuse of battery raw materials. This strategy could serve as a blueprint for Europe and help secure long-term resource requirements as well as minimise the environmental impact of the transport sector.
7. From material to recyclate
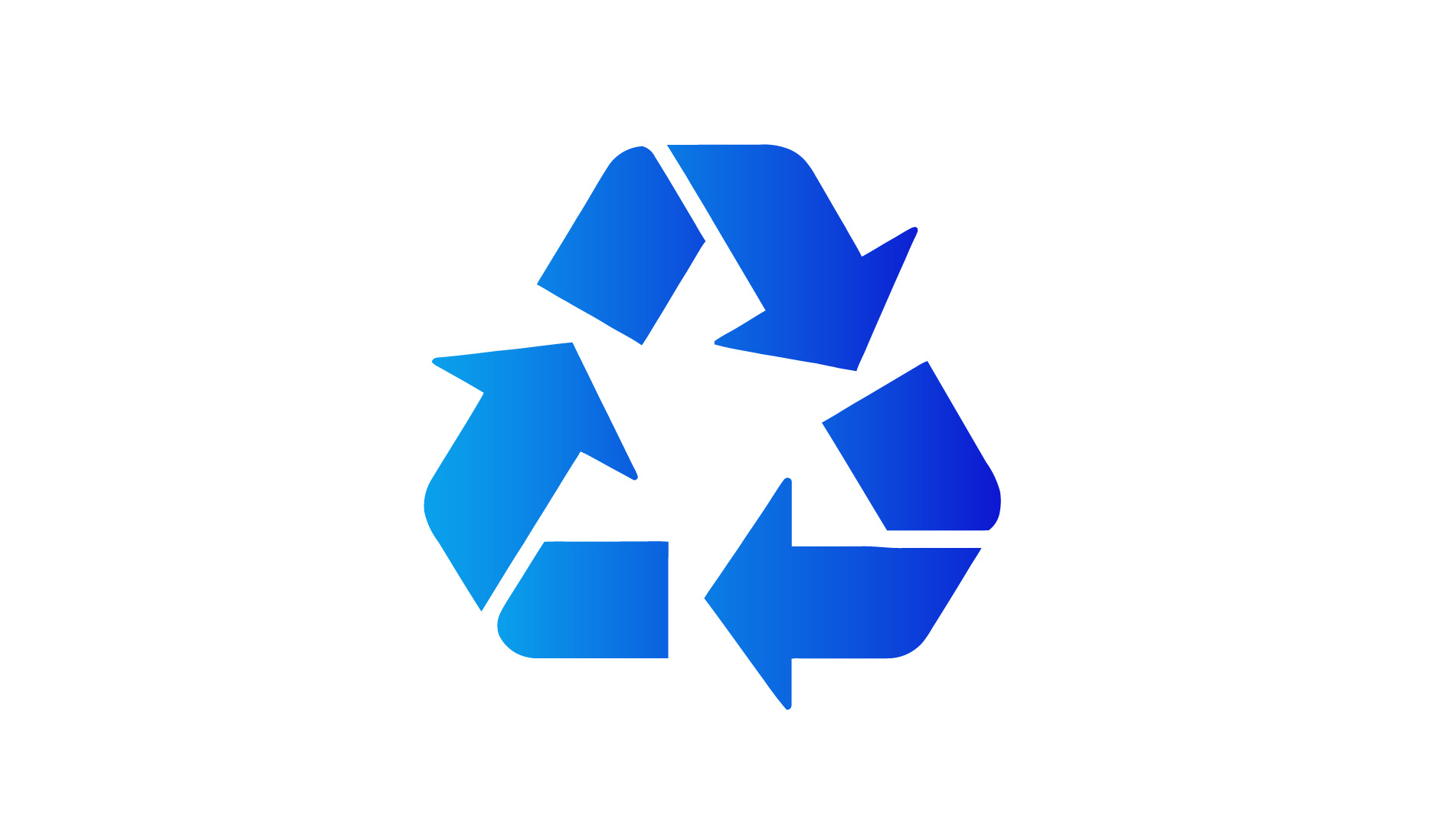
When a vehicle is charged with green electricity, most of the emissions it causes are due to the materials used in construction. 85 percent of construction materials are already declared as recyclable in Europe today – however, the resulting recyclates are still used far too little. This is where the EU’s proposed End-of-Life Vehicle Directive, which prescribes a recyclate-quota of 25 percent, should take effect. Before this can be achieved, a number of technical prerequisites have to be met, such as the separation of composite materials and value chains by type and, above all, the supply of end-of-life vehicles themselves, millions of which are sold abroad, sometimes illegally. In order to make progress here, companies need to focus their design methods more strongly on the requirement of circularity and, for example, reduce the mixing of materials in order to ensure improved purity. The ZEvRA project, in which five OEMs are working together to develop solutions for a vehicle made exclusively from circular materials, can serve as a blueprint here. Circularity requires that new technologies are developed for the extraction of materials from end-of-life vehicles and that the design focuses from the outset on assembly-disassembly with the aim of achieving recyclability.
8. Car recycling
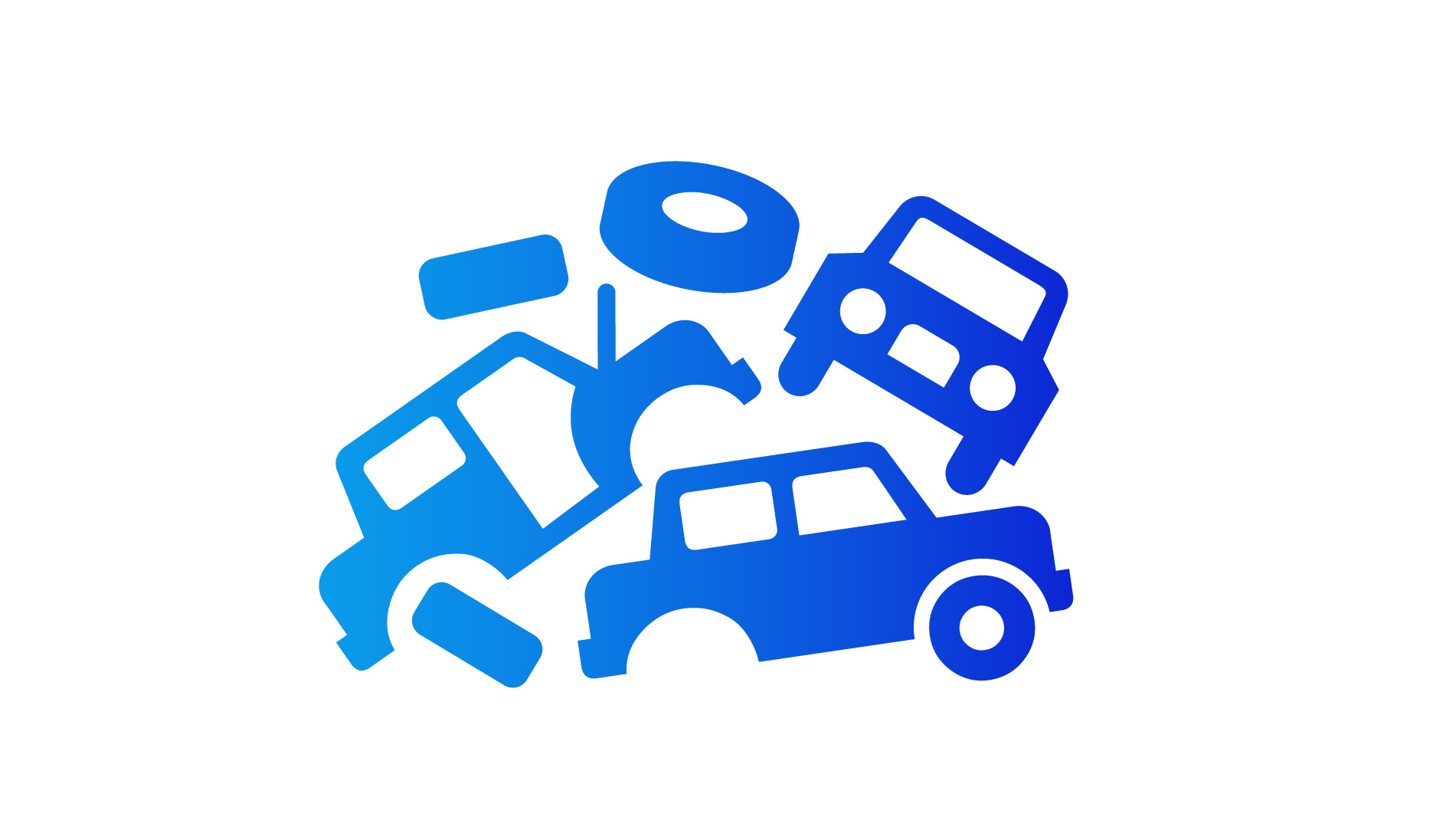
On the road to climate-neutral transport, the establishment of a circular economy in the electric car industry is fundamental. Numerous companies are working on solutions here. BMW's dismantling centre, for example, has long been making an important contribution to the recycling of vehicles and supports the International Dismantling Information System IDIS. This system provides information on the professional and environmentally friendly dismantling of cars for all authorised representatives worldwide. By supporting IDIS, each car manufacturer enables recycling companies worldwide to access detailed instructions and standards. This improves the dismantling and recycling of components. IDIS is especially important for electric vehicles as the handling of high-voltage batteries requires specialised knowledge and safety measures. In this way, the automotive industry is helping to ensure that batteries and other components are recycled efficiently and in an environmentally friendly manner worldwide.
9. Second-hand market
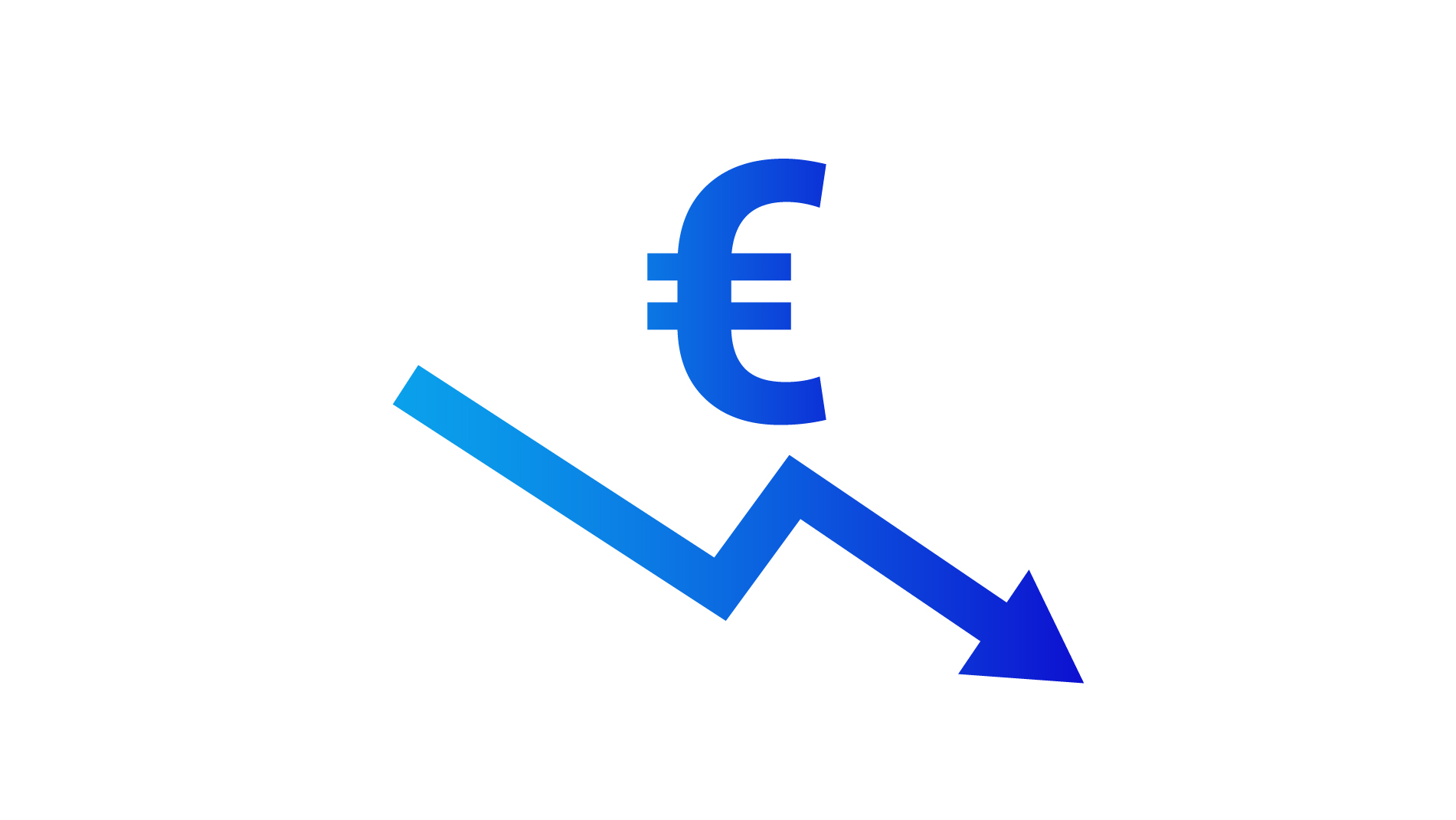
For e-mobility to have an impact, e-cars need to be sold. In addition to ‘Reichweitenangst’ or ‘range anxiety’ and the big price tag, it was previously the used car market which failed to gain momentum and so made investing in an electric car too risky for many. At first, prices for used cars were too high, and when they fell, the resale value also slipped into the realm of the incalculable. Leasing dealers also suffered: The residual values from back then no longer fit into today's market, as they are a loss-making business or increase the leasing instalment, which puts customers off. What's more, electric cars have developed so rapidly – in terms of drive systems, power electronics and batteries – that a model that is three or four years old is already outdated. There is now a solution to another obstacle. If there is any uncertainty about the condition of the battery (the most expensive e-car component), there is a battery check that can be carried out by the driver. New tools by various providers give information about the ‘health condition’ of the battery and the value it still has. The measurement results are certified and form part of the price calculation. However, if the battery is already exhausted, it can be sent to its second life in a regulated manner.
10. Standardisation
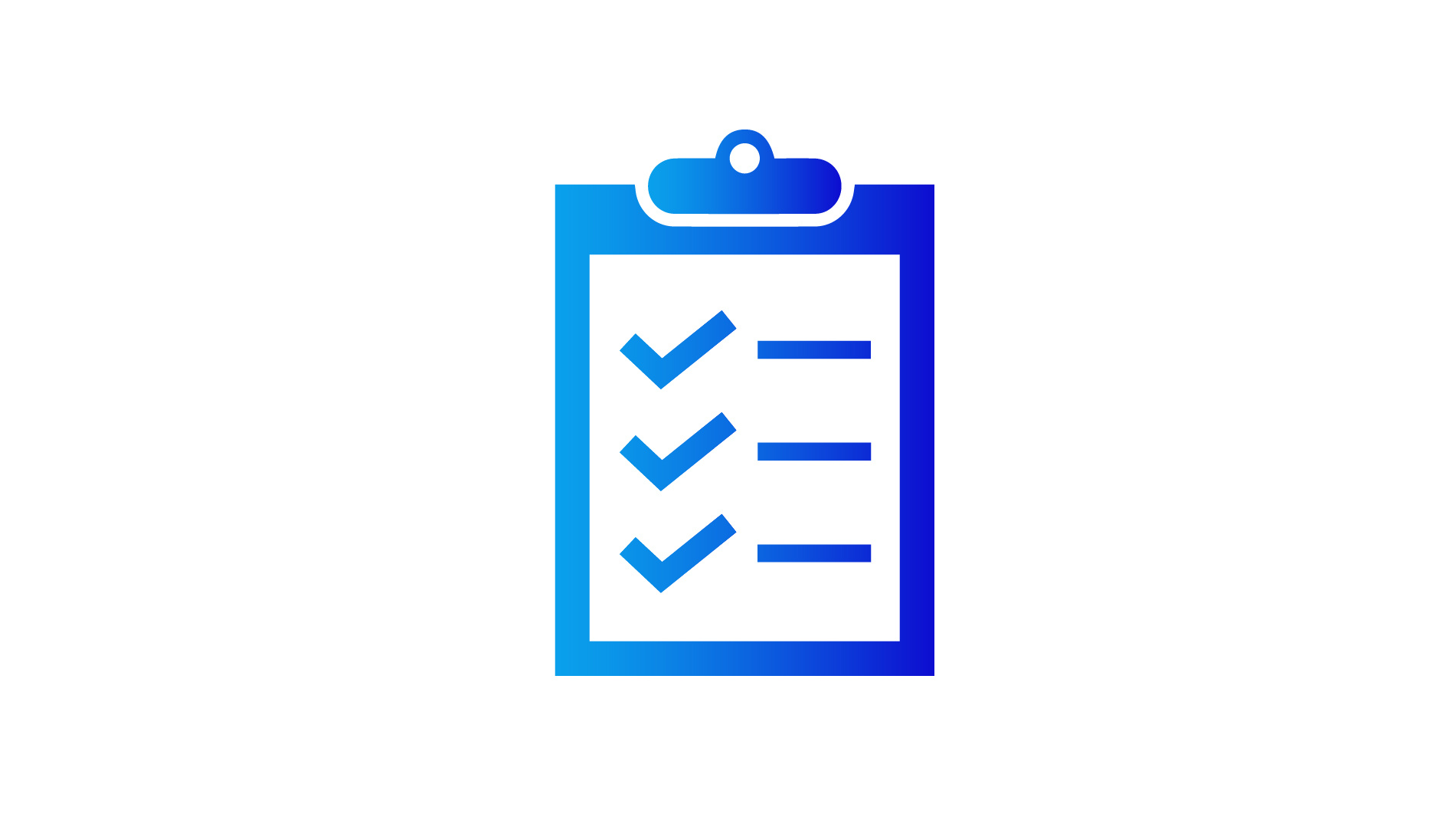
It is only through DIN-standardisation that innovations can enter the world of things in Europe, because only after DIN-standardisation can they connect to other things. Integration into global standards – there is a distinction between European and international standardisation – is also coordinated by the DIN headquarters in Berlin. Overall there are 37,500 experts who define norms for all industries. In the case of e-mobility, 95 per cent of standardisation takes place at international level. To date, around 250 e-mobility standards have been defined. They range from the definition of what actually constitutes an electric car, to safety concerns, to all manner of specifications relating to charging. Topics such as interchangeable batteries, bidirectional and inductive charging are still on the agenda. Gaps in standardisation when it comes to heavy-duty charging are currently being closed. Concepts for the infrastructure are currently being developed, including how to integrate standardised charging facilities in single-family homes or rental properties. And in practice, e-drivers are urgently calling for payment apps and cards at charging stations to be standardised, which needs to be addressed by the industry. Drivers can then use one system through the entire trip even on longer journeys without having to re-register. This topic exemplifies where the challenges of e-mobility lie: In order to find solutions, all parties have to work together, even if they have not been doing it so far. It’s up to all of them now: The automotive industry, the financial sector, electric suppliers. DIN is bringing them all to the table.
We would like to thank Dr.-Ing. Stefan Caba (EDAG Group), Dipl. Ing. Christof Kerkhoff (VDI – The German Engineering Association’s division for vehicle and traffic technology), and Corinna Scheu (DIN – Mobility Division) for the informative backgrounds discussions and good cooperation.