Reading time: 4 minutes
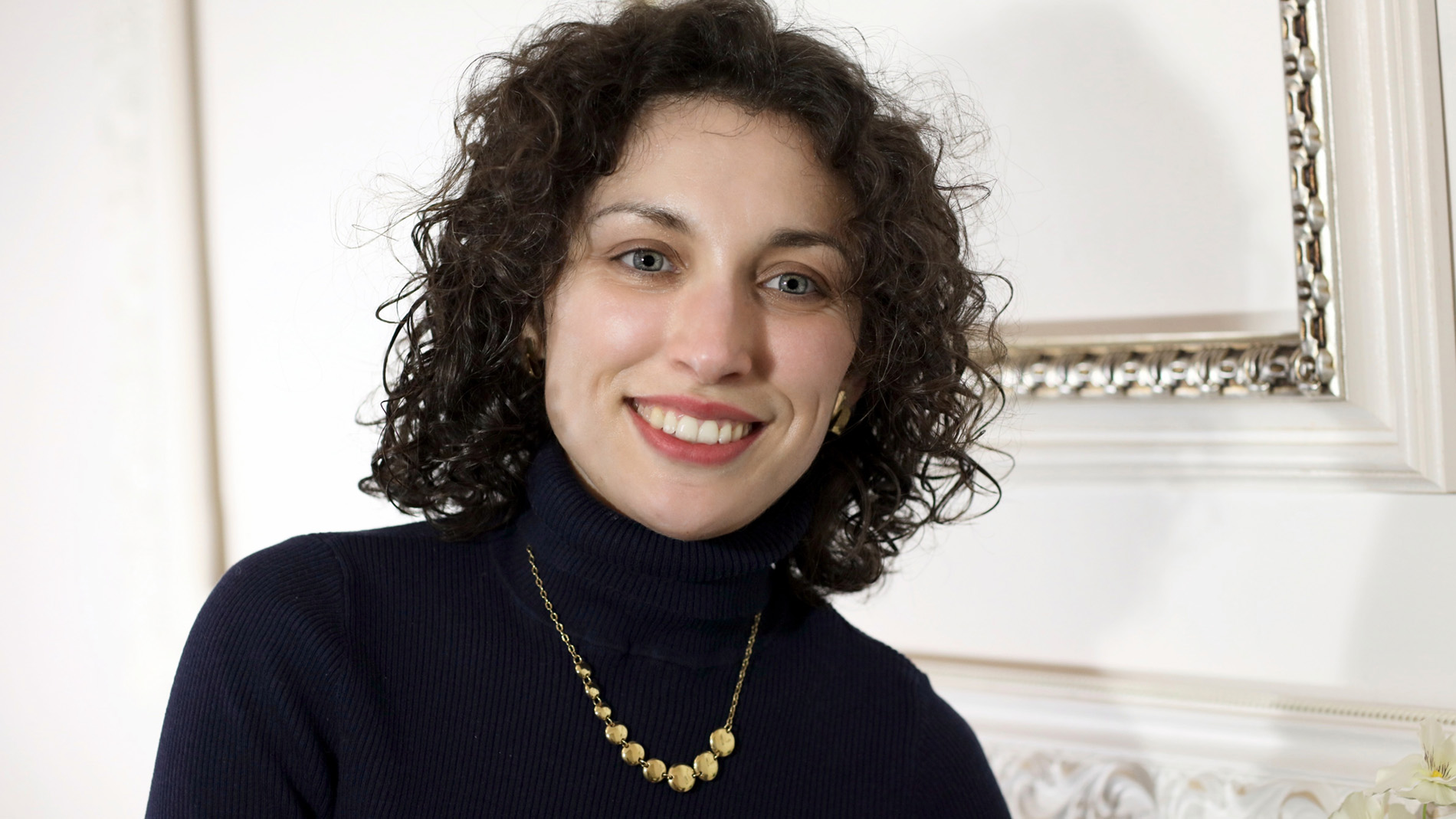
What does ‘cradle to cradle’ mean in the automotive market and aftermarket?
When considering emissions in the automotive sector, the first thing that comes to mind is the emissions during the use phase—tailpipe emissions. This has long been the primary focus, particularly for internal combustion engine (ICE) vehicles, where the largest environmental impact traditionally occurred. However, as we transition towards powertrains that are less impactful during the use phase, such as electric vehicles, it becomes crucial to adopt a holistic, ‘cradle-to-cradle’ approach. This approach considers all direct and indirect impacts across the entire value chain, from raw material extraction to production, use, and eventual disposal.
‘The cradle to cradle approach considers all direct and indirect impacts across the entire value chain, from raw material extraction to production, use, and eventual disposal.’
Currently, the manufacturing of an electric vehicle can be as impactful—if not more so—than the emissions generated during its use phase. In some cases, more CO2 is emitted in producing the vehicle than in driving it. This shift underscores the need to minimize the environmental impact of production and disposal processes. And if we look at other kinds of impact (such as natural resources depletion), we’ll find that the production of vehicles is one of the most resource-intensive industries.
In this context, the circular economy presents a unique opportunity. By reintegrating materials and components from the end of one product lifecycle into the beginning of another, we can significantly reduce waste and resource consumption. This can be achieved through various strategies, including recycling, but also through repair, remanufacturing, and reusing components. These strategies hold enormous potential in the aftermarket sector, especially for the complex components that are so prevalent in the automotive industry.
‘The strategies recycling, repair, remanufacturing and reusing components hold enormous potential in the aftermarket sector, especially for the complex components that are so prevalent in the automotive industry.’
By focusing on circularity, we not only reduce the environmental impact of production but also extend the life cycle of existing products, thereby decreasing the demand for new resources and reducing overall emissions. This approach aligns with the broader goal of achieving sustainability in the automotive sector and is essential for meeting emissions targets in a meaningful way.
When creating recyclability, it is essential not to use parts that cannot be recycled. Do you feel like the industry is making good progress on this issue?
Yes, the industry is making good progress on this issue. The European auto recycling value chain already delivers an exceptional reuse and recovery rate of around 95 percent. For cars, the recycling rate stands at a remarkable 85 percent, with an additional 10 percent of materials being repurposed for energy recovery. With the introduction of new EU regulations, this percentage is likely to increase further.
‘The European value chain for car recycling already offers an exceptional reuse and recovery rate of around 95 per cent. For cars, the recycling rate is an impressive 85 per cent, with a further 10 per cent of materials being reused to generate energy.’
From a research perspective, there is growing interest in the development of new composite materials, particularly those incorporating natural fibers. These materials offer the dual benefits of retaining desirable mechanical properties—such as high strength and low weight—while also being recyclable. Encouragingly, some of these innovative materials are beginning to be implemented in new vehicles, especially in interior components, signaling forward momentum in this area.
Additionally, significant efforts are being made in battery recycling, which is crucial as we shift towards electric vehicles. However, one area that could do with improvement lies in the steps preceding recycling—specifically, disassembly. Effective recycling requires that different components, often made from diverse materials needing specific treatment, are properly taken apart. The same principle applies to reuse and remanufacturing; it all starts with disassembly that is feasible and time-efficient.
This can only be achieved if designers consider disassembly at the very beginning of the vehicle’s lifecycle. Incorporating disassembly into the design process and providing detailed instructions, similar to those used for vehicle maintenance, is essential. Currently, this aspect is often missing from design practices, yet it is a fundamental pillar of circular design. By integrating these considerations early on, we can significantly enhance the recyclability and sustainability of automotive products.