Reading time: 1.5 minutes
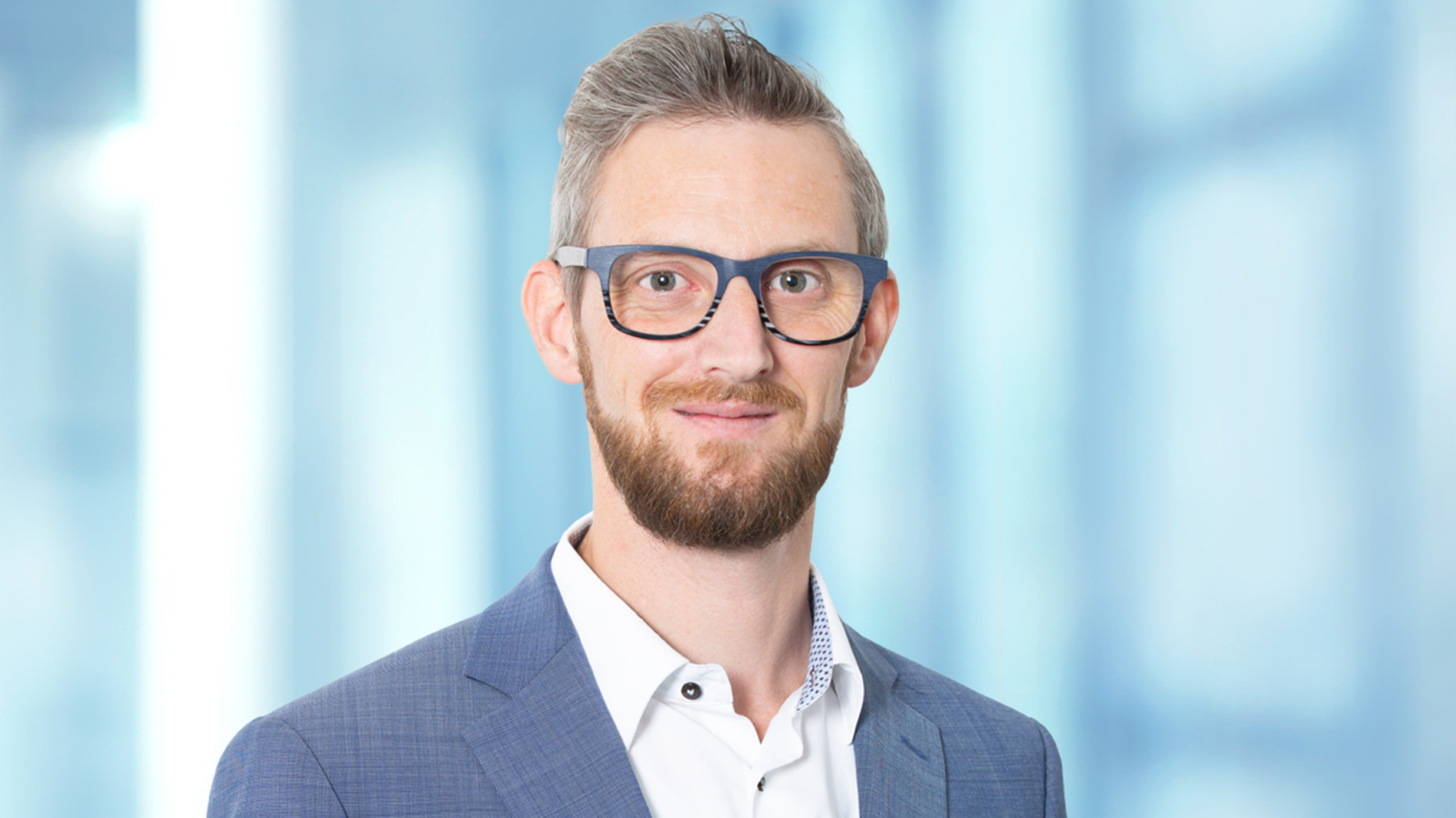
For the automotive and aftermarket industries, the circular economy is a critical tool for achieving emission targets. How can Knorr-Bremse contribute to this through industrial remanufacturing of used components in the truck sector?
With EconX®, Knorr-Bremse has created a brand for industrially reconditioned products. Remanufacturing not only saves material and energy, but is also a cost-effective and functional option for using older vehicles safely for a long time. Currently, Knorr-Bremse offers approximately 500 different EconX products, which are original, contemporary and sustainable.
What are the benefits of using remanufactured products?
The three main benefits of professional remanufacturing products are: Firstly, raw materials are returned directly to the cycle. Secondly, existing Knorr-Bremse products are given a second life through the EconX brand. And thirdly, these products extend the life cycle of older trucks.
Can you quantify the potential CO2 savings from remanufacturing?
We can show the CO2 reduction per part based on our Life Cycle Assessments. For example, in the production of an EconX SN7 tensioner, the use of remanufactured components reduces CO2 emissions by up to 44.9 kg. In 2023, Knorr-Bremse's remanufacturing activities in Europe saved 3,648 tons of CO2, 1,220 tons of material and 18.97 MWh of energy.